Investigating the Impact of Pallet Design on Plastic Pail Performance

Palletized unit loads are fundamental to the supply chain. These distribution systems, composed of pallets, packaging, and unit load stabilizers, play a critical role in ensuring the safety and efficiency of logistics operations. While significant research has been conducted on corrugated boxes used in palletized loads, the behavior of plastic pails under similar conditions has remained largely unexplored. Plastic pails, widely used for transporting various liquid and solid materials, introduce unique challenges due to their structural characteristics and load distribution behavior.
CPULD’s graduate student, Mary Paz Alvarez, conducted research focused on the interactions between plastic pails and pallet components, particularly the effects of pallet top deckboard thickness and pail location, with the aim of improving pallet design for safer and more sustainable transport of pails.
Pallets serve as a foundational element of unit loads, providing a stable platform during handling, transport, and storage. The design of pallets, including factors such as material choice, deckboard thickness, and structural integrity, can significantly affect the overall performance of the unit load. Traditionally, research has focused on optimizing pallet designs to support corrugated boxes; however, plastic pails differ significantly in shape, weight distribution, and structural resilience, making it necessary to study how these pails interact with pallets to ensure both product safety and load stability.
The primary objective of Alvarez’ research was to understand how plastic pails are influenced by two key factors: the thickness of the pallet's top deckboard and the location of the pail on the pallet. These variables are critical in determining the performance of the pails under load, including their deformation and compression strength. This research was conducted in two phases. In the first phase, the effect of pail location on a small-scale pallet segment was investigated, with pails placed in five different locations. This phase aimed to identify areas on the pallet where the pail might experience the greatest or least amount of deformation when under load.


In the second phase, the study focused on the two locations identified in the first phase as having the best and worst performance in terms of pail strength. Additionally, a third location was chosen based on a previous study involving corrugated boxes to compare trends across different packaging types. By testing pails in these key locations, Alvarez sought to investigate the relationship between pallet design and pail performance.
The results revealed several important insights into how plastic pails behave under different conditions on pallets. Firstly, both the thickness of the pallet's top deckboard and the location of the pail significantly impacted pail deformation, pallet deflection, and pail compression strength. Thicker deckboards generally provided better support, reducing pail deformation and improving compression strength. However, the experiments did not reveal a consistent trend between pallet deflection and pail failure, suggesting that other factors may also play a role in determining how and when pails fail.
One of the most critical takeaways of Alvarez’ research is that the location of the pail on the pallet has a statistically significant effect on its compression strength. Pails placed asymmetrically, particularly when one side is supported by a stringer and the other by a deckboard, experienced the lowest compression strength. This suggests that uneven support leads to increased stress on the pail, weakening its ability to withstand loads. Notably, pails supported at the edges of pallets showed up to a 40% reduction in compression strength compared to those placed at the center. This finding emphasizes the importance of pail placement on the pallet, with central placement providing the most stable support and reducing the risk of pail failure.
In addition to the location of the pail, the thickness of the pallet's top deckboard was also found to significantly affect pail compression strength. Thicker deckboards provided greater support, reducing pail deformation and improving load-bearing capacity. When the top deckboard thickness was reduced, the compression strength of the pail decreased by as much as 47%. However, it was noted that the difference between 0.5-inch and 0.625-inch deckboards was not statistically significant, indicating that beyond a certain thickness, further increases may not substantially improve pail strength. This finding suggests that while deckboard thickness is important, there is a threshold beyond which additional material may not yield proportional benefits in terms of pail performance.
Furthermore, the effect of the deckboard thickness on pail compression strength was found to be dependent on the location of the pail on the pallet. This interplay between pail placement and deckboard thickness highlights the complexity of designing pallets to accommodate different packaging configurations. While thicker deckboards generally enhance performance, their impact is influenced by how the load is distributed across the pallet.
Interestingly, while the thickness of the deckboards plays a role in pail failure, the experiments did not establish a consistent correlation. This suggests that pail failure does not just occur at a specific level of pallet deflection, pointing to the need for further research to understand the precise mechanisms that lead to pail deformation and failure under load.
The results of Alvarez’ study underscore the significant impact of pallet design on the performance of plastic pails. To ensure the safe transport of pails, packaging engineers must carefully consider the thickness of deckboards, the placement of pails on the pallet, and the load distribution. When reducing the thickness of the top deckboards for cost-saving or sustainability reasons, it is crucial to ensure that the pails retain enough strength to safely bear the load. Failure to account for these factors could result in pail deformation, product damage, or even safety hazards during transport.
In conclusion, this research provides a strong foundation for improving pallet design for plastic pails. By considering both pail location and deckboard thickness, designers can optimize pallets to minimize the risk of pail failure and enhance the overall stability and safety of palletized unit loads. These findings offer practical guidance for packaging engineers aiming to create more sustainable and efficient pallet systems while maintaining the structural integrity of the loads they carry.
Read the full article about this research project: https://onlinelibrary.wiley.com/doi/full/10.1002/pts.2672
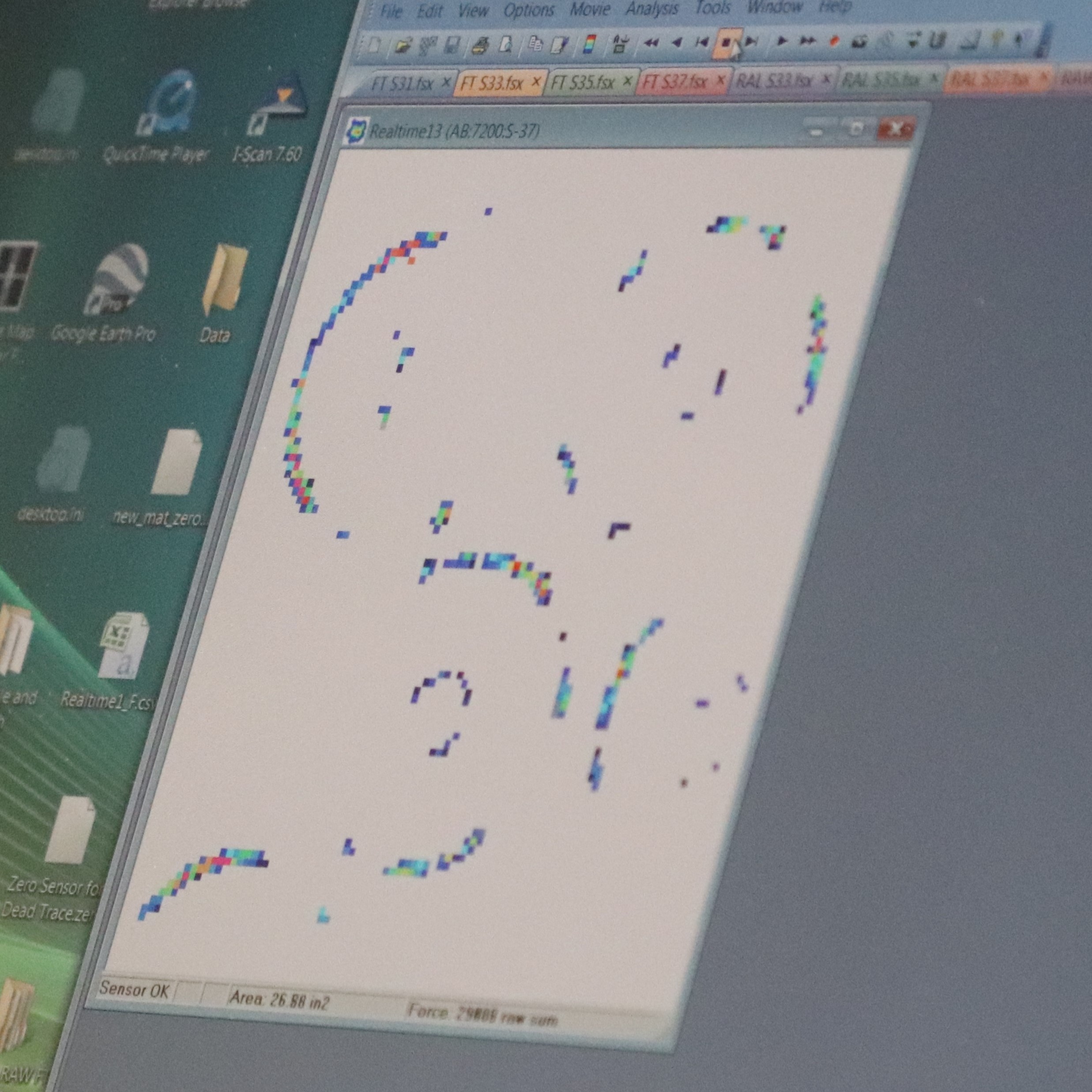