Research Highlight: Exploration of insulated shipping containers for cold chain distribution
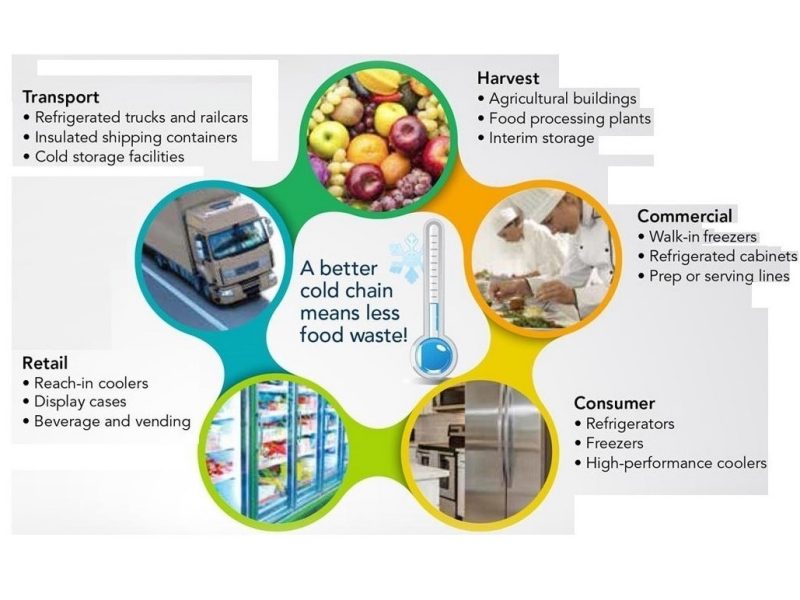
This study aimed to identify trends in cold chain packaging efforts as well as discover the materials and technologies used to successfully transport products at various temperatures. This project analyzed current trends and future innovations in cold chain processes and researched how they’ve contributed to developments in the industry. Undergraduate students in the Department of Sustainable Biomaterials, Alonda Johnson (Senior, Newport News, VA), Konnor Rafferty (Junior, Virginia Beach, VA), and Gracie Dixon (Senior, Richmond, VA) were chosen to conduct this research project.
The researchers looked into various technological advancements and how they have been used to improve tracking temperatures and shipments. The goal was to create a methodology that could be used to research cold chain insulated-container performance. The main objective of this study was to identify market-available, insulated-container systems that could maintain a temperature within 2°C and 8°C for at least 48 hours. This was done by conducting a market search/discovery, subsequent testing of the samples by closely replicating the ISTA 7E standard, and finally, analyzing all data points between the different materials and brands.
Given the complex nature of cold chain distribution, it can be difficult to regulate temperatures for long periods of time. Thermally insulated packaging protects products that need to stay within a certain temperature range to be considered stable and safe to use once they arrive at their destination. The temperature needs to be regulated, not only during transit, but also during the packaging process and storage. If the temperature is not kept within a certain range, sensitive products (such as food or pharmaceutical items) can spoil, and the customer will not be able to use them. Temperature trackers are necessary to confirm that the product was kept within the allowable temperature ranges throughout the packaging and shipping process.
The sponsor of this research project currently utilized corrugated boxes lined with 6panels of Expanded Polystyrene (EPS) foam in four different sizes: small, medium, large, and extra-large. The other samples that were evaluated were chosen based on criteria such as size, availability, qualifications, and materials (Table 1). As shown, a variety of shipping containers were gathered to explore their insulation abilities during this research. The 2-piece EPS, insulated liners, thermal panels, and recycled thermal panels did not come with corrugated boxes. To control for this, a C-flute Regular Slotted Container with an Edge Crush Resistance (ECT) of 40 lbs./in. was constructed using a Kongsberg Edge X24 computerized cutting table to fit each investigated container.
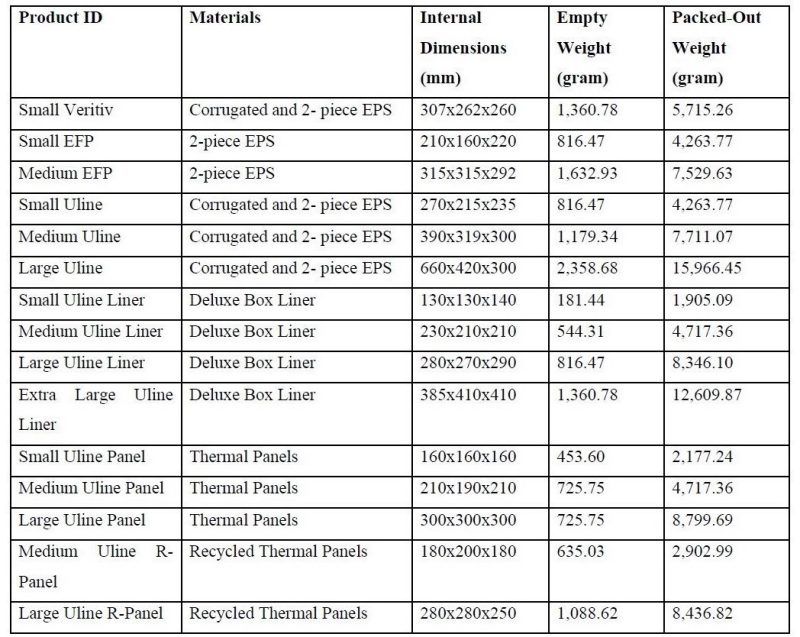
EPS is a polymer that is lightweight, ridged, and moisture-resistant (Image 2). These properties allow for several advantages during shipping. The lightweight property translates to lower shipping costs and a lower environmental footprint during the transportation. Since it is so lightweight, EPS can transport more volume of product by weight than most other insulating materials. Its rigidity allows the container to have a high compression strength value, and this added strength is especially important for products that are fragile and cannot be used if damaged. EPS’s moisture resistance properties help protect the corrugated box by creating a barrier between the box and any condensation created by the cooling mechanisms used during shipment.
The liner inserts are 1-piece systems made from two parts, an exterior liner and an interior foam. The exterior, a metalized LDPE, creates a moisture barrier and has high oxygen permeability. These properties protect the corrugated box from moisture but also ensures circulation throughout the packaging. The interior, a polyurethane foam, has high insulating and cushioning properties. Its insulating property allows the package to keep its temperature for an extended time. The foam will be able to absorb shock forces and potentially mitigate harm to the product. Overall, this solution is very lightweight and flexible (Image 3A).
The Recyclable Panel insert (Image 3B) is comprised of two different parts: liner and filler. The exterior is made from kraft paper. In the US, kraft is made from 50% recycled fibers and 50% virgin fibers. The filler is made from a blend of renewable plant-based components and starch. This mixture creates a moisture-resistant element to the container. This option is also curbside recyclable, thus making it the most sustainable container that was tested.
Bluetooth temperature probes, by the brand Onset, were placed throughout the shipping containers to track the change in temperature throughout the container. The inside probe was used to primarily determine if the products were staying in the desired temperature range and the outside probe was used to determine if the container itself was staying in the desired range. The disposable sensors turned red if the temperature surpassed 8 degrees Celsius.
Throughout the testing of cold chain containers, many variables were discovered that could alter the results of the tests. Some presented themselves immediately, such as the temperature of the chamber and which products were used for insulation. However, other variables arose including the temperature of the cold packs themselves, the starting temperature of the simulated products, the amount of void fill, the amount of time spent packing boxes, and sensor variations/malfunctions/etc... Furthermore, in a testing environment, it is not possible to simulate the exact handling that packaged products will endure once in shipment due to supply chain variability. Taking these points into consideration, the results of this study are meant to act as comparative data to each other and not as validation results to use for shipment in a cold chain.
After conducting the study, the four insulated containers that performed the best included: EFP EPS, Uline Recyclable Panel, Uline Panel, and Uline Liner (Table 2). However, the Uline Recyclable Panel was ruled out because of the condensation that was produced and leaked through to the corrugated board, damaging the quality of the box. The Uline Panel Small showed potential to do well for 24-hour shipping, but all other sizes failed under normal conditions. The Uline Liner performed well for almost all sizes, and it has the widest range of sizes. It could possibly be a good candidate for frozen shipments rather than refrigerated ones as it was able to drop the temperature quickly and did not heat up quickly.
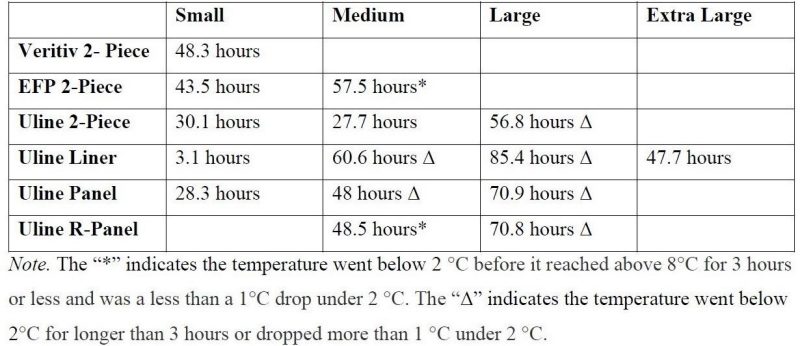
But, the top recommendation from this study is the EFP 2-piece EPS. This container performed best with an alternative pack out that used less materials. This lighter anticipated weight translated to a lower impact on the environment and shipping costs. The main material used was EPS, which is lightweight, durable, and affordable. The durability adds extra strength to the container, which can be especially helpful during shipping.
In total, 64 test trials were conducted for a total of 3,025 hours and on four different materials across three brands. Many of the containers tested, even if they failed the 48-hour tests that were conducted, have the potential to be utilized in other ways, such as in shorter shipping timeframes, or in a frozen shipping system. Stemming from the results of this study, there are several other topics that should be investigated. Possible future studies could focus on the pack-out process itself, look into the effect of the type of corrugated board that is used to ship these temperature-controlled packaging systems, and explore more sustainable alternatives.