Research Highlight: Initial prototype of a simplified method to evaluate fastener properties for pallet joints
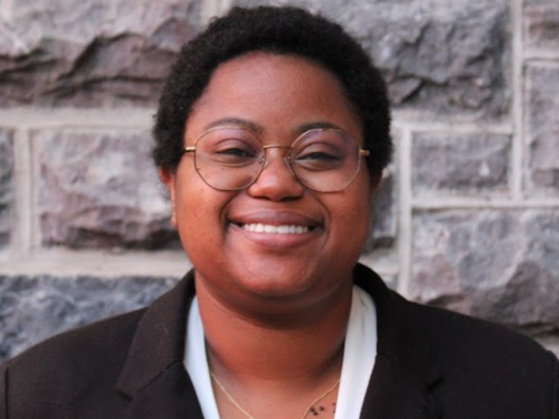
To determine the strength of fasteners in joints on a pallet, it is generally necessary to conduct an incline impact test, which involves a pallet colliding into simulated forklift tines. While this method accurately predicts pallet performance, it is time-consuming and expensive. Individual fastener strength can be estimated by conducting a Fastener Quality Analysis (FQA), which includes a Morgan Impact Bend Angle Nail Test (MIBANT), and then using that data to mathematically predict the fastener’s performance. However, there is no existing testing methodology that can be used to evaluate the dynamic performance of individual pallet joints. The purpose of this study was to ideate a testing apparatus that could simplify testing the strength of the fasteners in pallet joints.
CPULD undergraduate student, Alonda Johnson (Senior, Newport News, VA), was selected to conduct this sponsored research project (Image 1). During this project, Johnson designed and manufactured a prototype of a small-scale tester to be used in measuring dynamic pallet joint strength. She then compared the data collected from her new testing equipment to the currently-used incline impact tester and outlined recommendations for future research.
Failure in pallets happens most commonly at the joints. Several factors contribute to what type of failure occurs and how soon it occurs. The type and number of fasteners used in the joint are definitely factors, as well as the strength and placement of said fasteners. Factors such as the diameter of the fastener head, the depth of penetration into the pallet joint, the distance the fastener is from the edge of a board, and the distance between fasteners also affect the strength of a pallet joint. In comparison to 2.5-inch nails, 2-inch nails can increase pallet rigidity by 36%, strength by 17%, and decrease end-splitting of deckboards by 50% if the number of nails per pallet is increased by approximately 50%.
Fastener performance can be estimated by calculating three values: fastener withdrawal index (FWI), fastener shear index (FSI), and head pull-through resistance (HPT). FWI is characterized by the amount of resistance that a fastener experiences when being withdrawn from a material. FSI is the fastener’s resistance to lateral deformation from shear forces. FSI is calculated using the wire diameter and its resistance to impact. The resistance to impact is derived from the fastener’s bend angle, determined using the Morgan Impact Bend Angle Nail Test (MIBANT). Finally, HPT is the tendency of the fastener to embed deeper into the material than originally placed.
The test samples created closely mimicked the section of a pallet that consists of a top deck board and two stringers. The sample was constructed by using pieces of wood that were similar to the dimensions and wood types used in a standard 4-stringer pallet. The incline impact test determines a pallet’s resistance to lateral impact forces such as interactions with material handling equipment like forklifts and pallet jacks. That test can simulate impacts from any part of a forklift on any part of a pallet. This first prototype testing equipment that was designed was a vertical impact tester (Image 2).
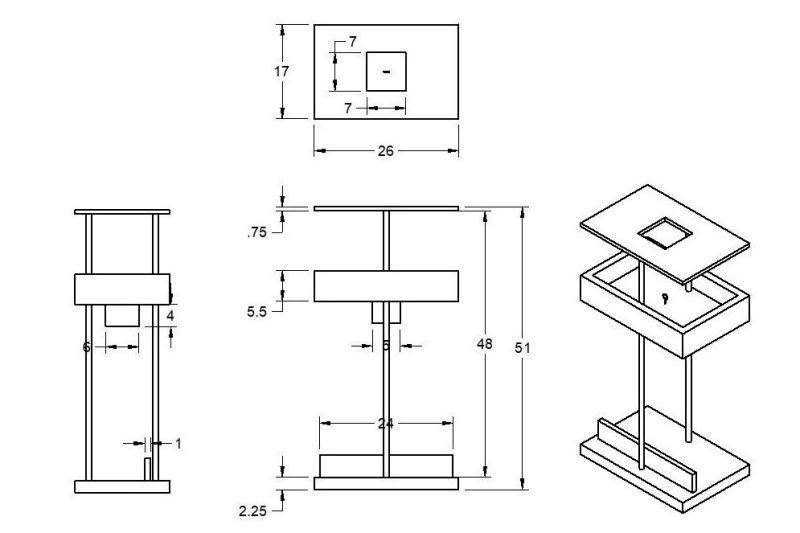
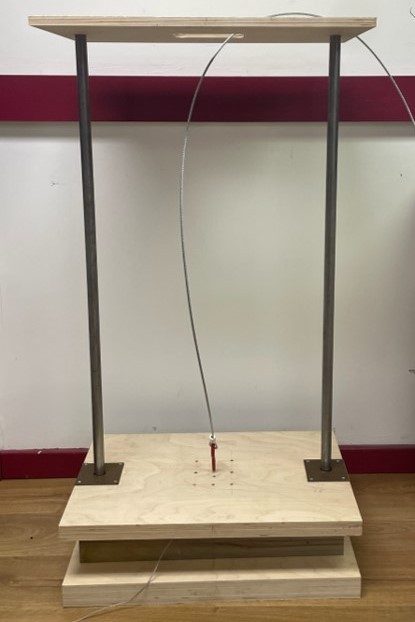
This prototype tester was designed to isolate the vertical component of the incline impact test. This is done by mathematically correlating the kinetic energy at various speeds of the incline impact test to the vertical impact test. The testing hazard on the sliding platform was to simulate the front of the shank of the forklift tines impacting the pallet during handling. To perform the vertical impact test, an accelerometer was attached to the sample. The calculated weight was applied to the sliding platform of the testing equipment. The platform was then lifted until there were 24 in. between the sample and the testing hazard. The sliding platform was then released and impacted the sample.
For future research, a new iteration of the prototype must be designed. Better vertical trajectory must be ensured, as well as better control of the height of the moving platen. A rubber stopper should be added to each of the rods to aid in switching the samples by allowing the sliding platform to stay elevated.
This project concluded with the recommendations for future iterations of the testing equipment design and conducting more comprehensive validation and verification testing. Future studies should be designed to compare quantitative data, such as cumulative kinetic energy, to the incline impact tester results. This would allow for analysis not only of how precise the data is but also of its accuracy. CPULD is currently in the process of designing and manufacturing the next iteration of this testing equipment.