Featured Research: Measurement of hazards experienced by pallets during material handling
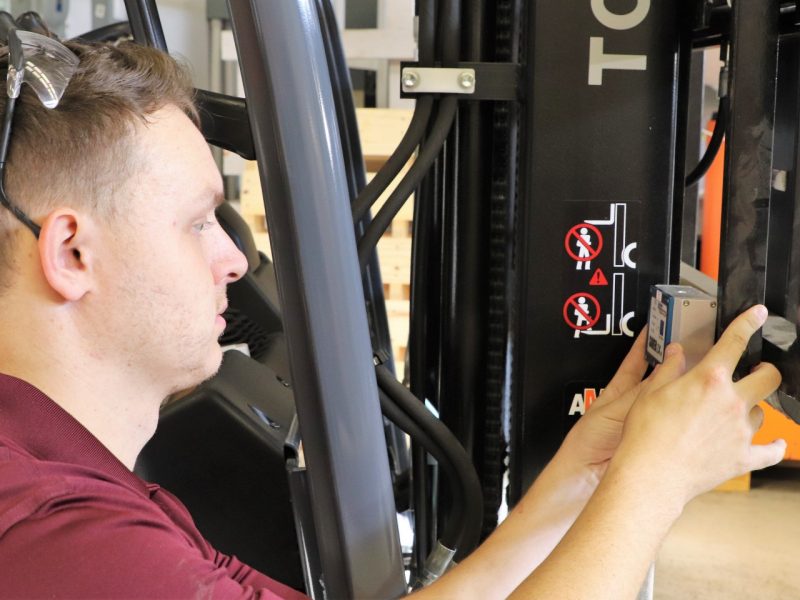
Recently graduated CPULD alumni, Clark Sabattus (Master’s Degree, Arlington, TX), researched “Measurement of Hazards Experienced by Pallets During Material Handling” for his Master’s project (Image 1). The objective of this research project was to investigate the intensity of the vibration and horizontal shock impacts that forklifts exert on pallets during material handling. Although often overlooked, pallets can become costly for a company if not designed correctly for their specific supply chain. Forklifts are the dominant mode of material handling for palletized products, and they are responsible for the majority of damages experienced by pallets.
Despite the prominence of forklifts in the supply chain and their importance to pallet design, there is a lack of research focusing on the interactions between forklifts and pallets. It is important to be able to replicate what a pallet might experience in the field, so when testing in a laboratory setting, a company will be able to accurately gauge their pallet’s functional capabilities. The creation of a simulated material handling environment in 1993, named FasTrack, has aided in researching a pallet’s useful life. FasTrack simulates a pallet going through a series of trips, utilizing material handling equipment such as forklifts and pallet jacks. It was designed to replicate the environments that a unit load of products may travel through in the field in order to observe the common damage modes that may occur to a pallet.
The first study that investigated forklift handling in a laboratory setting was conducted in 2021 by Yu Yang Huang1, another CPULD alumni. His project investigated gas, reach, and electric forklifts. Each forklift went through a series of handling scenarios to determine the effect of different variables such as unit load weight, speed, road conditions, and sensor location. A follow up study by Borocz2 was conducted, also in 2021, which expanded the number of investigated forklifts and proposed a PSD profile that could be used during laboratory simulation of forklift handling.
These two research projects provided a basic understanding of the vibration levels seen during forklift handling and how different variables affect that vibration; however, there was still a lack of research investigating the vibration and shock environments during material handling in a field environment. Thus, the objective of this research project was to characterize the vibration environments and the horizontal shocks experienced by pallets during forklift handling in different types of facilities.
Forklifts in multiple facilities were instrumented with data loggers (Lansmont SAVER 3X90 and 3D15) to measure the acceleration peaks, g’s of shock impacts, duration of impacts, random vibration intensity, and RMS(g) values during forklift handling in the field. This field data was collected from three different types of facilities: a distribution center, a manufacturing facility, and a pallet manufacturer. The mean peak acceleration values in the field were relatively similar between facilities. The values were the lowest for the pallet manufacturer (0.264g) and highest for the distribution center (0.353g). The acceleration values at 98% also revealed that peak accelerations experienced by the forklift can be as high as 1.65g.
The mean acceleration values found during this project are lower than what was recorded by Huang et al. in the laboratory environment (Huang et al., 2021). An explanation for the differences between the field and the laboratory measurements could be the presence of “dead head travel” where forklifts travel without carrying any load. This type of movement can produce higher frequency vibrations that, when averaged into the data, can alter the observed vibration profile.
The intensity of impacts during forklift handling were also assessed in the same facilities. The Saver 3x90 dataloggers were attached to the forklifts behind the carriages holding the fork tines. The summary of these acceleration/shock duration values for the investigated facilities are presented in Table 1. Over the four-week investigation, only 25 shock events occurred at the distribution facility, while 245 shock events were of interest at both the LTL and manufacturing facilities. The results of these measurements showed that LTL facilities recorded the highest average shock impacts of all the facilities investigated with an average acceleration value of 4.74 g’s and an average shock duration of 7.42 msec. When the harshness of handling in the field was compared to the handling intensity found during FasTrack simulations, it was determined that the simulated intensity in Fastrack is only slightly harsher than what was observed in the field. The results indicate that the FasTrack simulation is a good representation of the handling processes used in the field.
References:
1. Huang, Y. Y., Horvath, L., & Böröcz, P. (2021). Measurement and Analysis of Industrial Forklifts Vibration Levels for Unit Load Testing Purposes. Applied Sciences, 11(7), Article 7. https://doi.org/10.3390/app11072901
2. Böröcz, P., & Singh, S. P. (2018). Measurement and analysis of delivery van vibration levels to simulate package testing for parcel delivery in Hungary. Packaging Technology and Science, 31(5), 342–352. https://doi.org/10.1002/pts.2327