Research Highlight: Evaluation of temperature control units' supply chain distribution routes and the damages experienced
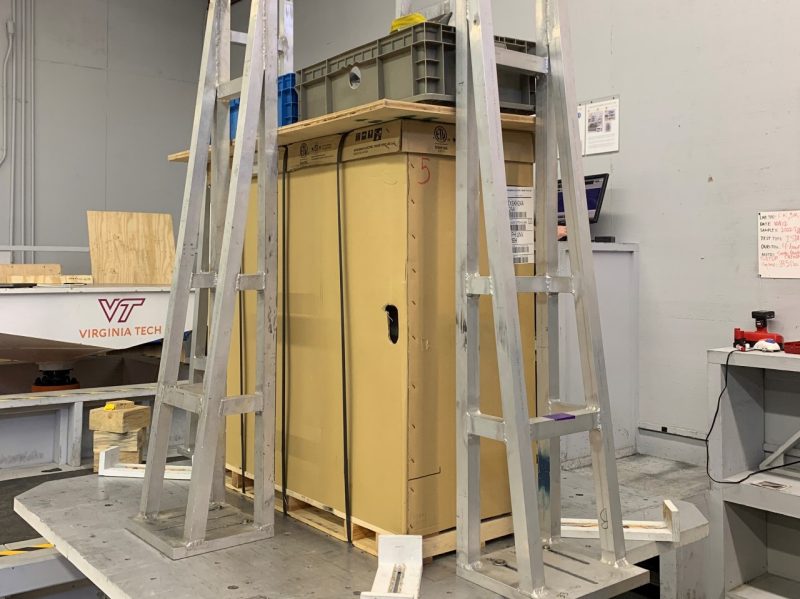
One of the world’s largest manufacturers of major home appliances sponsored an undergraduate research project for students in our department for the fall semester 2022. Undergraduate students Shak Kataev (Senior) and Collin Kennedy (Junior, Chesterfield, VA) were selected to evaluate various packaging systems used to ship heat pumps and air handlers. A final report was presented to the sponsor summarizing their findings and giving analysis of the packaging systems’ performances.
Six units were provided for testing purposes. The units included two types of products (air conditioning units and heat pumps) from three different brands: Midea, Mitsubishi, and Trane. All units were shipped in corrugated packaging sleeves. Both Mitsubishi units and the Trane air conditioning units were transported on pallets. All units arrived with some level of plastic strapping for additional containment strength. However, the bottom of the Midea AC unit arrived disintegrated. This unit was deemed untestable as containment of the unit was already compromised, so only five units ended up being used for this project (Table 1).
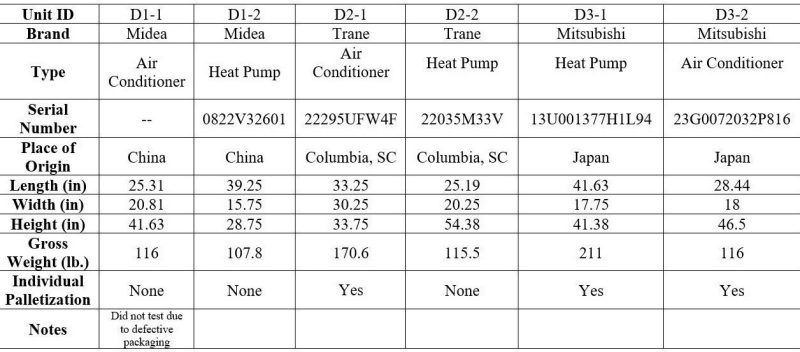
The specific procedures used to test the Midea, Mitsubishi, and Trane heat pumps and air conditioning units followed the ISTA 3E standard. This standard serves to mimic movements and stresses surrounding loading, full truckload shipping, and unloading individual packages. In real life, each step carries risks of drops and falls. The ISTA 3E standard is the perfect testing process to replicate the mechanical stresses, vibrations, and potential damage experienced by a package during shipment to and from distribution centers. Packaging systems that pass these tests can then be certified as such and utilized for global distribution.
The units tested were large products (all more than 100 lbs.) shipped in large boxes. Each product was unitized by itself; it was its own unit load and not made part of a larger load. Due to the packages’ large sizes, individual manual and mechanical handling was the most optimal. Inclined impact tests were conducted to simulate drops or shocks that could be experienced while being handled by a forklift or by hand. The manual handling of the units needed to be simulated with particular emphasis on the failures that can occur; to simulate a failure in manual handling, shock testing was conducted to simulate the dropping the unit (Image 2).
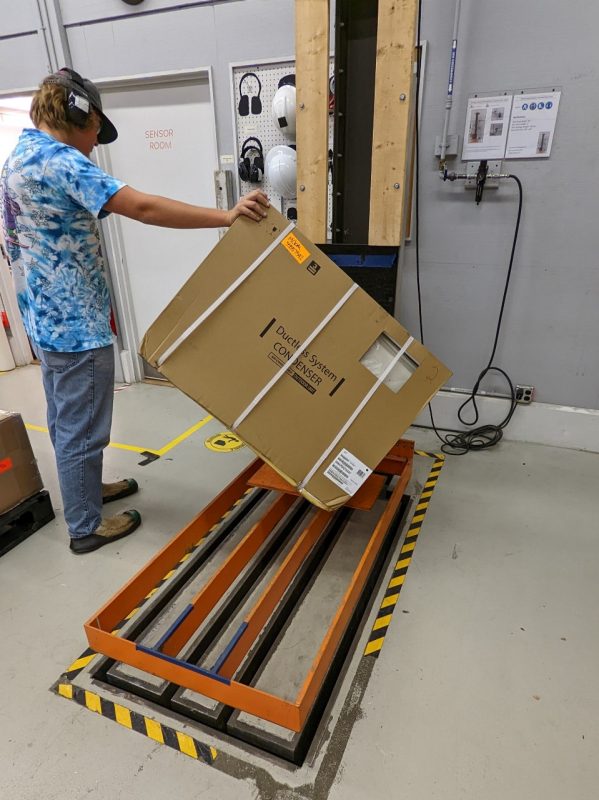
Custom testing sequences were developed for each product using the ISTA testing standard to best mimic the transport sequence of the product being shipped in its package. No test sequence followed the same order, but each unit was tested in a way that the standard outlined. The units were measured, weighed, and properly inspected before any testing procedure began. Then, in general, stability tests, mechanical handling by forklift, drop tests, impact tests, and more drop tests were conducted. The packages were then vibrated under various profiles, and subjected to stacking conditions as they would experience in a warehouse. Finally, more vibration tests and drop tests were conducted before each package was taken apart for inspection.
Each of the units and their packaging systems were visually inspected for damage, discrepancies, and anything of note that may have occurred during the testing phases. Corrugated packaging was measured in length, width, and caliper. Polymer foams and polymer straps were weighed and measured for caliper. Curbside-recyclable components were fully assessed and weighed as a percentage of the total packaging. Pallets, under the palletized units, were similarly inspected; their stringers and deck boards were measured and examined for damage. Some units came with polymer bags containing components important to the units’ operation. And, some units came packaged in large polymer bags just under the corrugated sleeves which were large enough to cover all of those boxes’ various items.
All units sustained some damage to their corrugated packaging. Tears and punctures were common among all tested units. For the remaining Midea product, this packaging damage was all that was incurred. However, the Trane units had shifted on the pallets, which resulted in lots of damage to all corners and straps. Also, once the packaging was removed, there were dents and scratches in both of the Trane products (Image 4). The Mitsubishi units also sustained damages to their packaging, pallets, and the products themselves. As these units were designed to be installed in homes by professionals, it was not able to be determined if the units would still function; however, none of the observed damages seemed severe enough to be the cause of product malfunction.
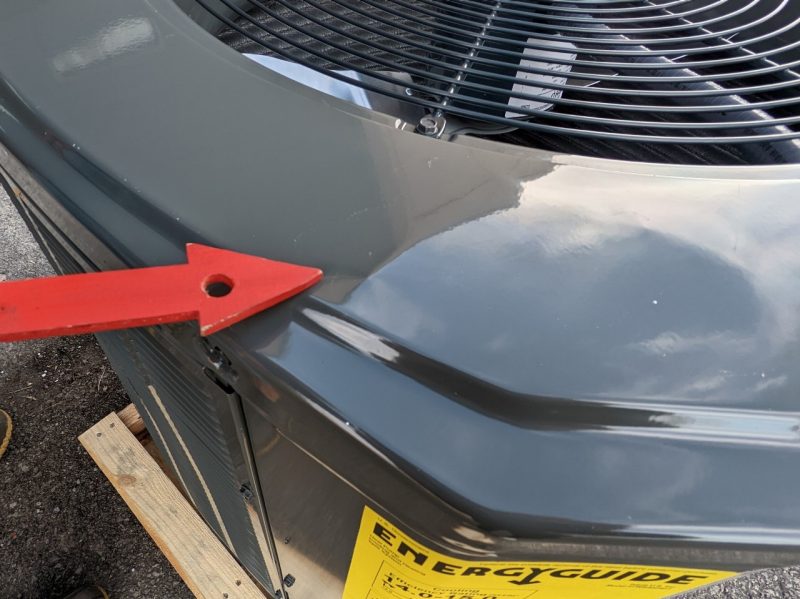
The students also created a breakdown of the packaging materials by recyclability and what proportion of the overall packaging was recyclable. Packaging made from forest/wood products, such as corrugated fiberboard, laminate, wood, and other derivatives was deemed curb-side recyclable. Fiber-based packaging was separated into its own category. Packaging components made from recyclable plastic polymers was also deemed curb-side recyclable. Polystyrene (PS), metal, unlabeled plastic components, instructions, installation and operations manuals, and accessories were not deemed recyclable. All recyclable materials were calculated as a percentage of the total packaging and then as a percentage of each unit’s total weight (Table 2).
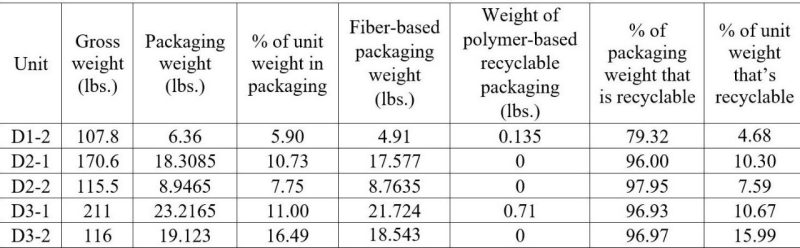