Research Highlight: Predicting the joint stiffness of wooden pallets assembled with lag screws and carriage bolts
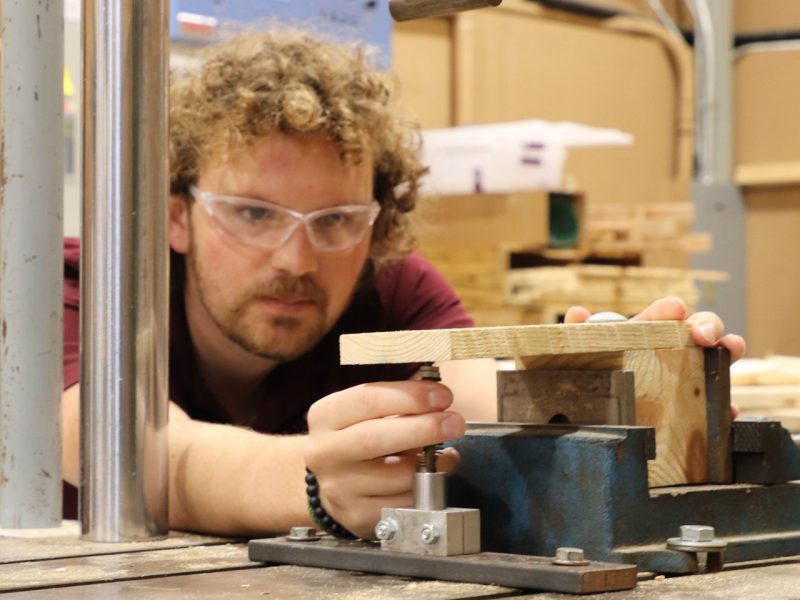
In order to design pallets that can be used safely, the load capacity of the pallet needs to be measured or calculated. Although the load capacity of a pallet depends on a multitude of factors, the stiffness of the joints between pallet components has a major influence on overall pallet load capacity. Heavy-duty pallets are often assembled with alternative fasteners such as bolts and lag screws. Currently, the effect of these alternative fasteners on joint stiffness is not understood; this limits the use of these fasteners by the industry. Therefore, the objective of this research was to investigate the stiffness of pallet joints constructed using alternative fasteners such as bolts and lag screws. Master’s student, Joe Keller (2023 alumni, Charlottesville, VA), was selected to work on this research project which was sponsored by The Pallet Foundation / National Wooden Pallet and Container Association.
In order to predict joint stiffness, head embedment stiffness, shank withdrawal stiffness, and rotational stiffness were measured for each joint type. The objective of this project was to determine the head pull-through, shank withdrawal, and edge crushing stiffness of pallet joints made from carriage bolts and lag screws and using different species of wood. Two different species of wood, including southern yellow pine and red oak, were used for the study. Half of the pine samples were tested in a green condition, while the other half were tested at a 19% moisture level. The oak samples were only tested in green condition.
A model had been developed by previous researchers to predict the measured rotational stiffness of pallets by which nails were used. The model consists of three stiffness values that must be calculated, including: head embedment stiffness, shank withdrawal stiffness, and moment rotation stiffness. This project’s researchers followed the original model.
For the head embedment test, specimens were assembled by inserting the investigated alternative fastener into a pre-drilled hole in the wooden board. The board with the alternative fastener was placed upside down on I-beams and clamped to prevent bending. A sensor was placed under the head of the alternative fastener to measure the amount head embedment. The MTS equipment was used to pull the shank of the alternative fastener and cause the head to embed into the wooden board (Image 2).
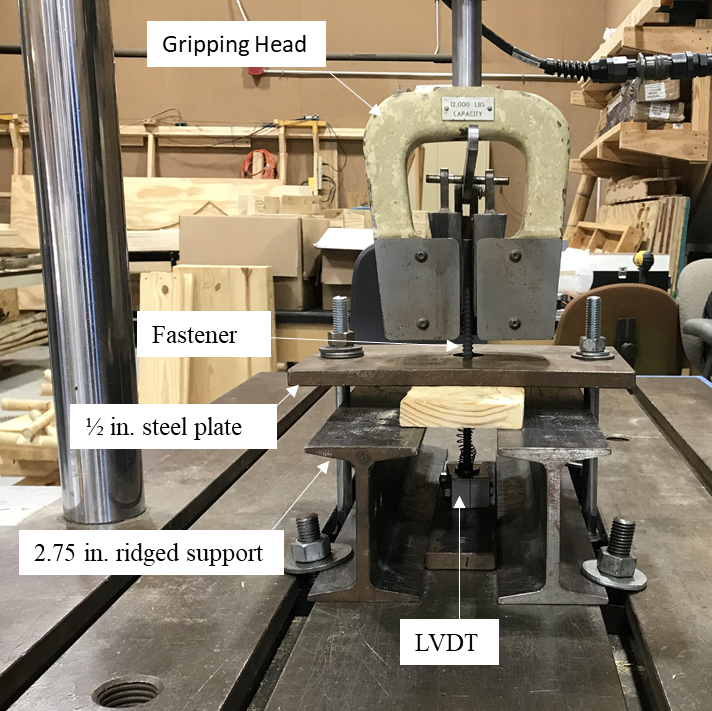
The next test performed was the shank withdrawal test. The setup involved screwing alternative fasteners into properly conditioned wooden blocks. The blocks were supported on each side and a sensor was placed against the head of the alternative fastener in order to accurately measure nail movement relative to the block. A steel bar was pushed by a wooden yoke which was attached to the MTS equipment, and a load was applied.
The final test that was performed was a moment rotation test to find the third stiffness measurement needed to complete the model. These tests gave the researchers the edge crushing stiffness – basically the crushing that the pallet joint will experience. Different species of wood have different amounts of crushing because of their cellular structure. So, different species needed to be tested to give accurate estimates. Deckboard samples had alternative fasteners screwed into predrilled holes which were used to attach the deckboards to the side grain of the blocks. The samples were then rigidly clamped to the base of the MTS machine, and a sensor was placed to measure the deflection of the deckboard joint during testing (Image 3).
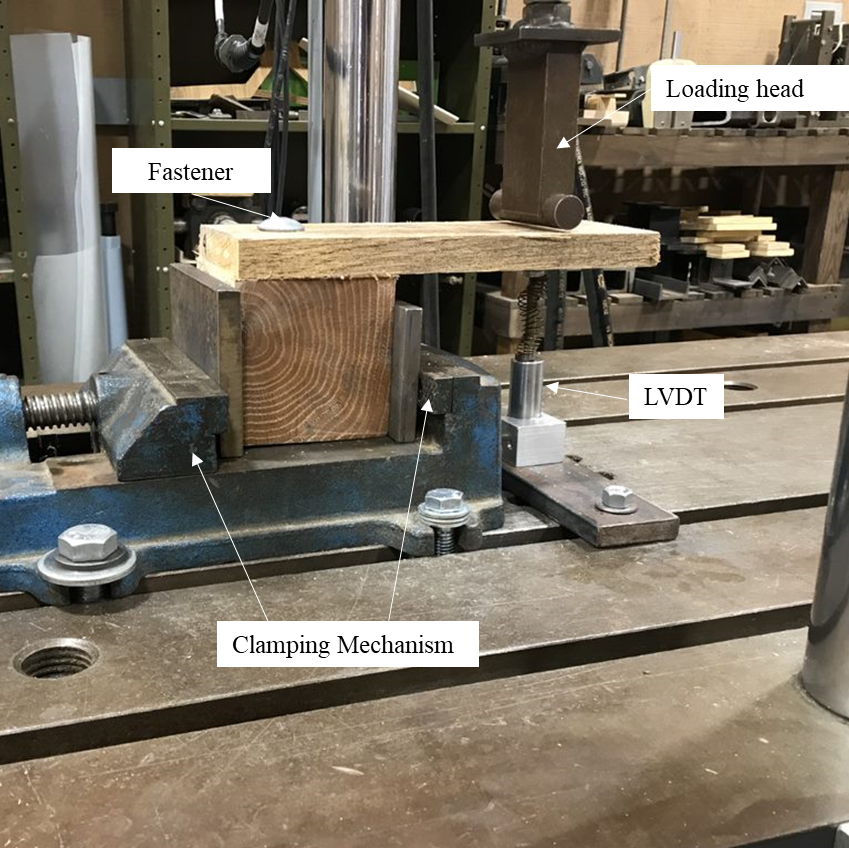
Overall, this study suggested that using carriage bolts and lag screws will provide greater stiffness than using nails in pallet joints manufactured from green oak, green pine, and KD-19 pine. The size of the fastener used in a pallet joint had a direct effect on the stiffness of each pallet joint. The larger the size of the fastener, the larger the head embedment and shank withdrawal stiffness. This study found that if green oak is used in pallet construction with lag screws or carriage bolts, it will provide stiffer connections than green pine or KD-19 pine with the same fastener types. KD-19 pine provides a slightly greater stiffness then green pine, but this was not seen as statistically significant. The head embedment stiffnesses investigated for the two fastener types (lag screws and carriage bolts) were similar enough to not be seen as statistically significantly different during analysis.
The results of this study will be included in the Pallet Design System (PDS) software in order to allow pallet designers to design pallets using bolts and lag screws.