Research Highlight: Undergraduate research project testing a sustainable, paper-based alternative to plastic stretch wrap
Image 1. Highlight Brands Synergy 4 High Profile Wrapping Machine applying new, sustainable, paper stretch film
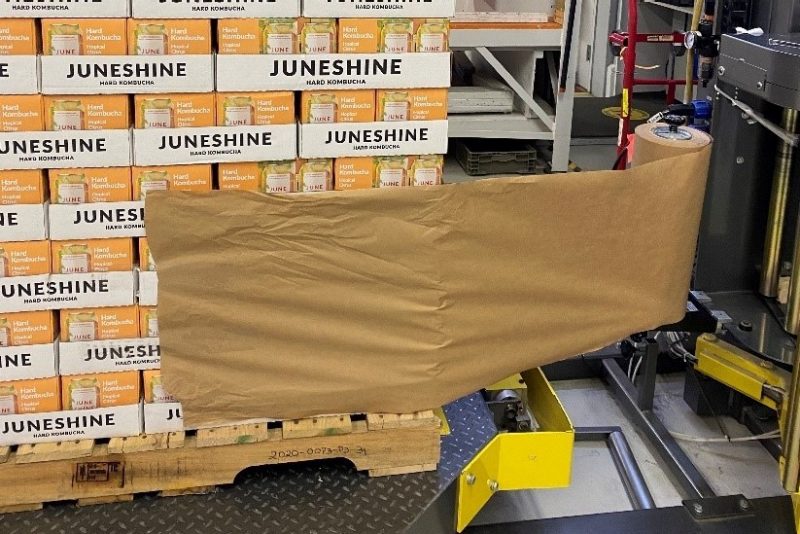
Image 2. Unit load wrapped with typical plastic stretch wrap film.
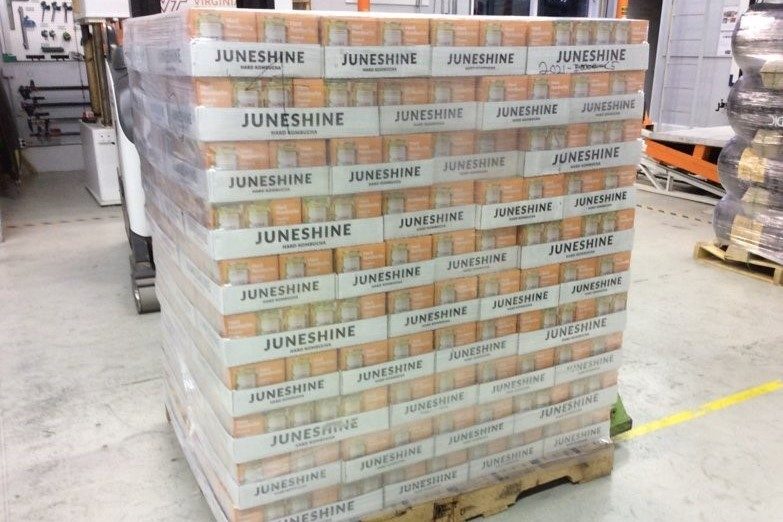
The packaging industry has recently started to take steps to address concerns about the environment regarding waste and pollution because packaging is estimated to make up 40% of the 250 million tons of total annual waste, and it makes up 50% of the total plastic waste globally. Packaging companies are trying to create eco-friendly packaging, which includes edible, bio-based, and biodegradable materials obtained from renewable resources. Although, the industry created 125,000 tons of bio-based packaging materials in a recent year, the majority of the 100 million tons of packages were still made from petrochemical-based plastics.
To exemplify tangible advances in sustainable packaging development, packaging companies have taken strides to alter plastics and focus on similarly functioning alternatives. In particular, the international packaging world has taken an active interest in sustainable stretch films (Images 1 & 2). This research project was sponsored by Westrock. Undergraduate students, Gracie Dixon (Junior) and Shak Kataev (Senior) were selected for the project. The students were supervised by Saewhan Kim who is an MS student studying sustainable packaging. The goal of the project was to evaluate the potential of an alternative type of sustainable paper wrap to be used as a load stabilizer.
This series of experiments focused on testing unit load stability with two different wrapping materials: typical plastic LLDPE stretch film and a new, stretchable, paper film. The tests conducted during this experiment were an incline impact sway test, a 22-degree tip test, a rotational edge drop test, and a series of tests within the ISTA 3E standard of testing unit loads.
Different wrapping patterns were used to determine how the films would be applied to the unit loads. These patterns are called recipes. The chosen recipe is determined by the vertical speed of the spinning carriage, the amount of overlap, the amount of pre-stretch, the number of wraps on top and bottom, and a film force multiplier. These variables factor into the unit load’s stability after it is wrapped.
Identical unit loads were wrapped with four different recipes of the new paper film, and as a control, another unit load was wrapped with a plastic stretch film, and they were all tested the same. The unit loads that were wrapped with the paper film were evaluated for the new film’s potential as a viable alternative to the plastic stretch wrap. Measurements of the total sway and total slip were taken throughout the entire experiment.
During the impact tests, the unit load’s sway and slip increased with each impact until the plastic wrap failed to contain the unit load. At that point, product trays ripped through the plastic wrap and fractured the stacked unit load. Comparatively, the plastic film stretched but suffered no corner damage, while the paper wrap tore at the corners of the pallet where the paper wrap overlapped the products trays and the pallet, but it did not fail entirely as the plastic-wrapped unit load did. Ultimately, the plastic wrapped unit load failed at the 4.12 ft/s impact speed while the paper wrapped unit load remained mostly intact, except with the bottom corner tear (Images 3 & 4).
Image 3. Showing a plastic-wrapped unit load failure during incline impact tests.
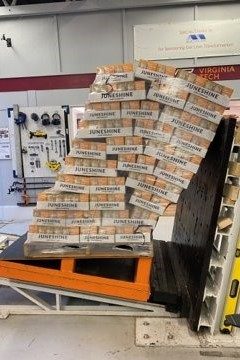
Image 4. Showing a paper-wrapped unit load failure during incline impact tests.
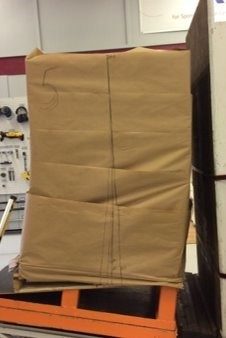
This study showed that during the Incline Impact and 22-Degree Tilt Tests, the paper wrap performance was superior to plastic stretch film. This indicates that sudden stops are better-sustained by the paper film than plastic film. However, the Rotational Edge Drop Test results indicate the plastic film can handle more limited drops. The overall unit load was very slippery, which resulted in sliding during certain tests. Ultimately, this could have been one of the biggest factors in this research. If the product trays had been manufactured from a different material, there would have been a different coefficient of friction.
Once the paper film began to tear on the corners, the unit load became unstable. The tears increase in length and spread over repeated impacts as the tension acquired during the wrapping procedure is lost. Since the corners were the biggest failure during the paper film testing. This could be prevented by adding corner stabilizers to give more protection.
Although the paper wrap has a potential to be an effective load stabilizer for certain types of unit loads, further research will have to be conducted to fully understand the limitations of this technology.