Research Highlight: Undergraduate research project evaluating the correlation of the containment forces of stretch wrap at the corners versus the sides of unit loads
Image 1. Highlight Brands Synergy 4 High Profile Wrapping Machine.
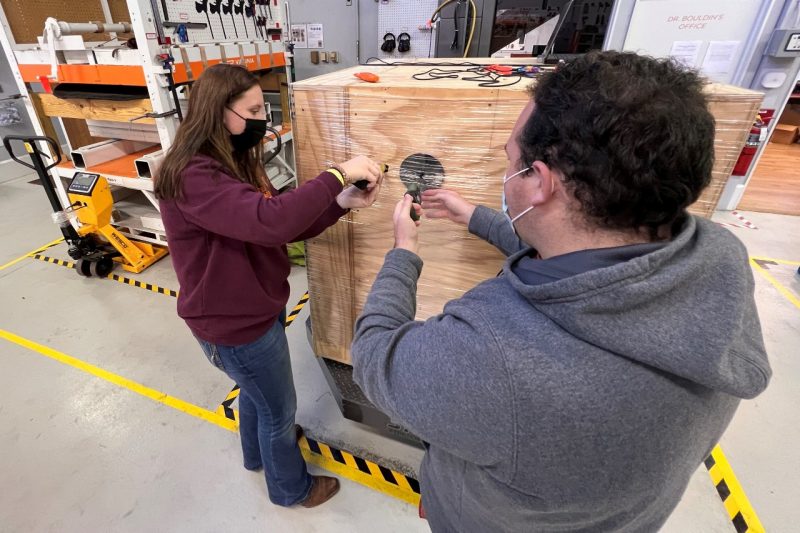
The movement of products has created a single world market connecting developing countries to first world nations. One of the problems that has arisen is making sure products arrive undamaged. When transporting products, they are commonly bundled together and placed on a pallet, which is called a unit load; unit load stability is crucial for the safe transit of goods. To this end, 65% of unit loads are commonly wrapped with stretch film.
The current standard for selection and use of stretch films is ASTM D 4649, which is one of the only regulated ways to compare one stretch wrap to another. The only test that reflects containment force on a unit load requires the user to pull a plate that was placed behind the stretch film outward. The stretch film itself provides the unit load with containment force, which is the technical term for how much force is required to maintain stability. Containment force is measured in pounds and there are different ranges of containment force needed depending on the unit loads’ weight.
This research project was designed to evaluate how the containment forces measured at the corners of a unit load correlate to the containment forces measured at the sides of a unit load, based on various stretch wrap factors such as pre-stretch, overlap, and number of layers – and how these variables impact the amount of film needed to stabilize the unit load. This undergraduate research project was sponsored by White and Company and the students selected to work on this project were Gabby Brophy (Junior) and Michael Harris (Junior). Both of these students are studying Packaging Systems and Design at Virginia Tech.
Image 2. Rigid test unit load with a length and width of 48 inches and a height of 50 ¼ inches constructed of plywood and lumber. Shows load cell located on side of unit load.
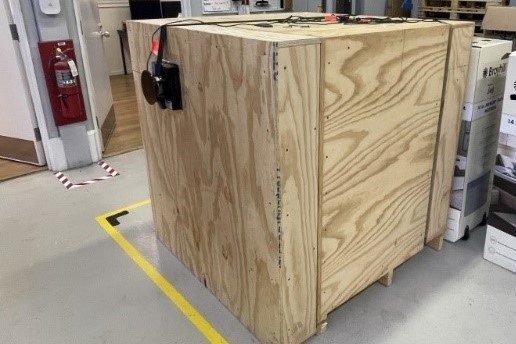
The researchers created a rigid test unit load constructed out of plywood and lumber. This test unit load was built as a one-piece structure designed to allow forklift handling (Image 2). To measure the containment forces provided by stretch wrap, the researchers utilized a Highlight Industries portable film cell testing kit comprising of three 100 lbs. max load cells. Two of the load cells were installed under the detached freestanding corner of the cube (Image 3) to measure the corner containment force. The third load cell was positioned to the side of the unit load, 10 inches from the top and 18 inches from the back of the cube. (Image 2). The data was recorded and analyzed using the Highlight Industries portable film force system.
Image 3. View of corner containment testing area - the 2 load cells are located 10" from the top and bottom of the unit load.
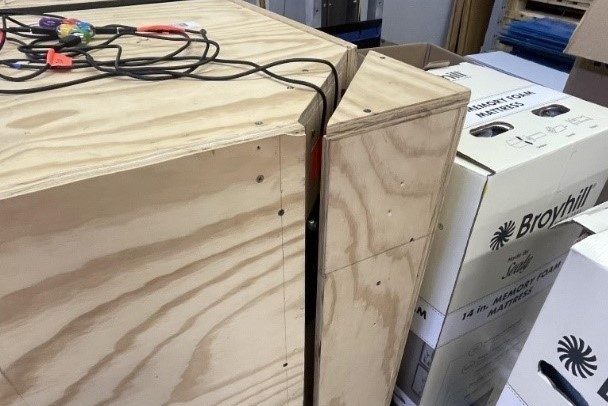
The results of the collected data demonstrated a correlation between multiple factors. The testing variables of the experiments were: the effect of layers, the effect of overlap, the effect of pre-stretch, and the effect of the overall stretch. The students evaluated how each these affected containment force and how each variable affected the total amount of stretch wrap used.
When the number of layers increased, the measured containment force increased for all scenarios. The greatest increase, of 19.69%, was found for the corner containment when the number of layers increased from 1 to 3. When the percentage of overlap between the different film layers increased, the amount of containment force also increased. The greatest increase, of 19.61%, for the corner force measurement, was found when the overlap was increased from 29% to 74.6%. This shows that as more layers are added to the unit load, the containment force will increase exponentially.
However, as the pre-stretch setting on the machine increased, the containment force decreased. This makes sense because, as the film gets thinner through the pre-stretch process, less containment force can be applied to the unit load. While the overall stretch had a negative effect, it was minimal.
From all of the testing done, one of the most significant findings was the correlation of 1 lb. of compression force measured on the side, from the ASTM pull plate method, correlated to 8 lbs. of containment force on the corner load cells. This project allowed the packaging students to gain more experience with the stretch wrapping equipment and get hands-on experience in determining the effect that the various factors had on containment force. The results of these experiments will be used by the sponsor to expand the capabilities of their unit load design software called Best Load.