Updates and upgrades to CPULD equipment
Image 1a. Unit load tester in the distribution lab.
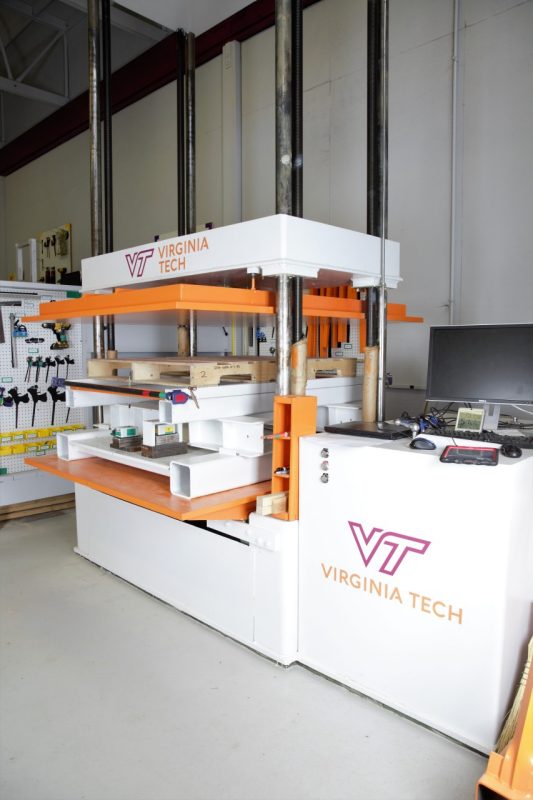
Image 1b. Upgraded software for the unit load tester.
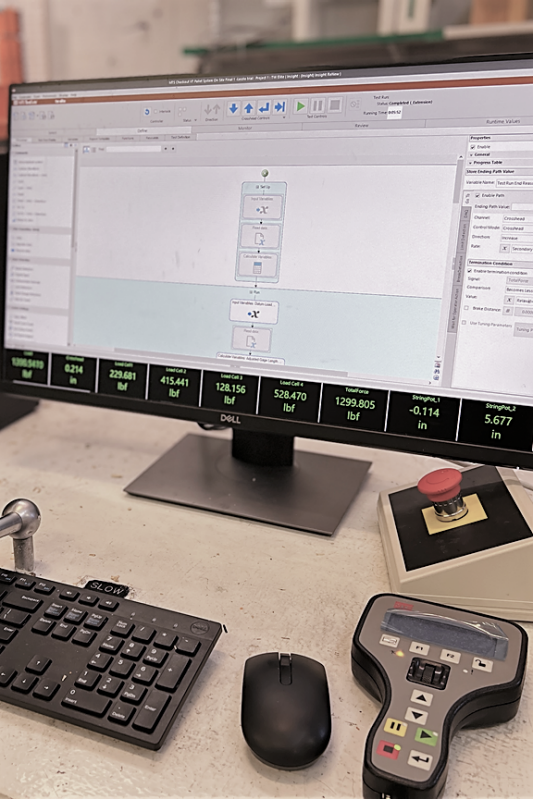
CPULD has been able to upgrade and/or replace many pieces of equipment over the last year.
One of the major upgrades has been to the software running our unit load testing equipment. Our unit load tester was built in the 1950s by the Tinius Olsen company (Image 1), and it has been updated electronically a few times over the years. However, it has always been something we physically built or developed. Now, we've partnered with MTS to retrofit the whole control system with new, state-of-the-art capabilities. This new software has more built-in analysis capabilities. We’ll be able to conduct much more detailed analysis because the software is collecting more data, reporting more data, and can process all of the collected data itself, which will reduce the post-processing time.
The equipment was expanded our capabilities to monitor up to deflection points on the pallet without string potentiometers and the system has the ability to receive signals from up to 52 deflection monitoring devices. We’ve also added a camera to the equipment to record exactly what's happening while tying it directly to the data being collected. Historically, when we built the software ourselves, we have to do all the data crunching ourselves. Now we have MTS backing the software, we are exchanging the electric motor for a new one with better, fine-tuning capabilities, and while there were only two speeds available before, now we will be able to dial in any exact speed we need for testing. Another large change is that the current equipment wasn't designed to conduct creep tests with its rigid platen, but now we’ll have software that controls the part of the equipment that produces constant pressure as needed for the creep tests which reduces the test setup time.
CPULD was also able to purchase a new PDT-80 drop tester from Lansmont Corporation (Image 2). The new drop tester has a lot of fully automated capabilities which allows us to conduct drops on small packages faster and with greater accuracy. The lab also acquired high speed cameras with ProAnalyst video analyzer software that allow us to accurately record the orientation of the package when it hits the ground and also get information on the deformation of the box during the drop.
To expand our data analysis capabilities that lab acquired two Saver 3x90 and two 3D15 data loggers from Lansmont Corporation and purchased multiple go-pro’s gps units and night-vision cameras. These new capabilities allow our students to collect data from different transportation modes and conduct state-fo-the-art research on this field.
Image 2. New drop tester in distribution lab.
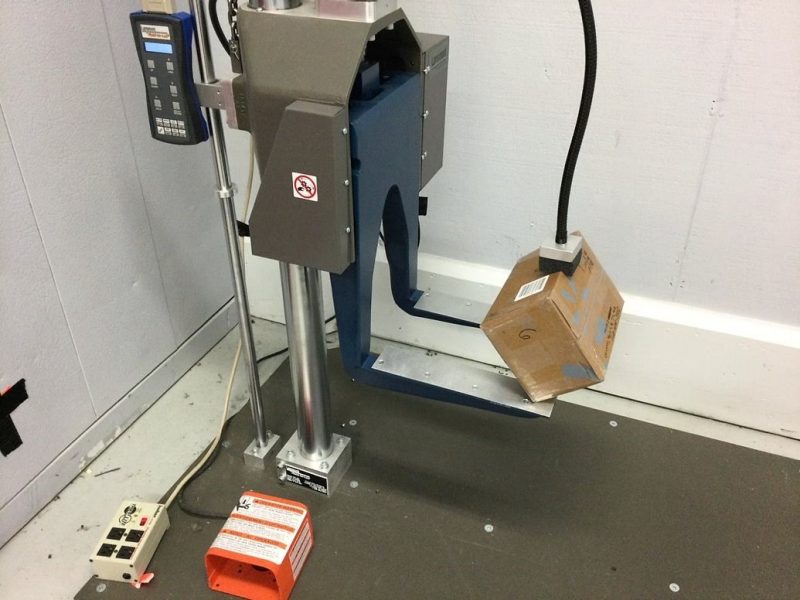
Another change around CPULD is the upgrade to the lighting in the FasTrack area of the lab. CPULD developed a unique, accelerated pallet durability simulation called FasTrack in 2000. This test can simulate decades of use to a pallet in a matter of months. To test a palletized unit load for durability and economics of use, we simulate rough handling. This accelerated rough handling can be achieved by using multiple devices employed in actual material handling systems. The protocol used is a modification of testing developed to simulate the use of pallets by the grocery dry goods industry. This portion of the lab used to be a dark, storage area, but due to the fact that FasTrack projects now make up twelve percent (12%) of CPULDs work, we decided to update the area in which these tests are conducted (Image 3). Other than making the space more functional, this change is also in-line with Virginia Tech’s long term sustainability mission and will significantly reduce our energy consumption and improve our environmental footprint.
Image 3. New lighting in the FasTrack area of the distribution lab.
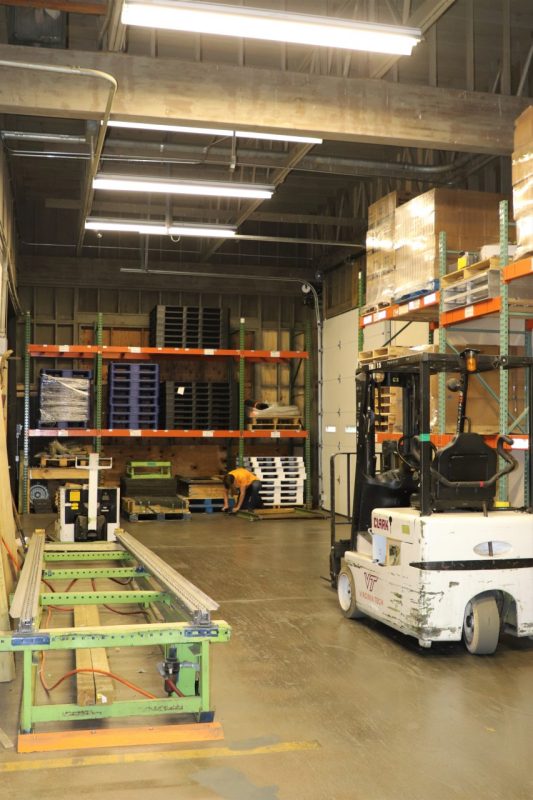
Finally, CPULD is currently working on establishing a new IAP membership related to unit load stability. Last year, the Center acquired a Lansmont TruMotion Horizontal Stability Testing equipment that will be the first unit load stability tester in any U.S. academic institution. This new equipment will allow us to lead the development of the first unit load stability testing methods in the U.S. This new capability and connected research will position the Center and Virginia Tech as global leaders in this area.
The share and importance of sustainable packaging is growing in the U.S. The Center and our packaging program are uniquely positioned to capitalize on this interest. Our long-term goal is to develop a new professional M.S. degree in Sustainable Packaging Design. The degree development will be completed by the end of 2022, so we hope to submit the new degree proposal by the end of the year.
As part of this degree’s development, a new advisory group was assembled that included major corporations such as General Mills, Seventh Generation, Pepsi Co, Loop, Pergis, and Atlantic Packaging, among many others. In the short term, the Center is working with the VT SBIO department to acquire technologies that will give our students the ability to design with novel packaging materials. We are also developing continuing education courses that we will be able to offer to the industry even before the approval of the degree.