Featured Research: The effect of forklift type, pallet design, entry speed, and top load on the horizontal shock impacts exerted during the interactions between pallets and forklifts
Figure 1. Forklifts used in the study (left to right: gas, electric, reach).
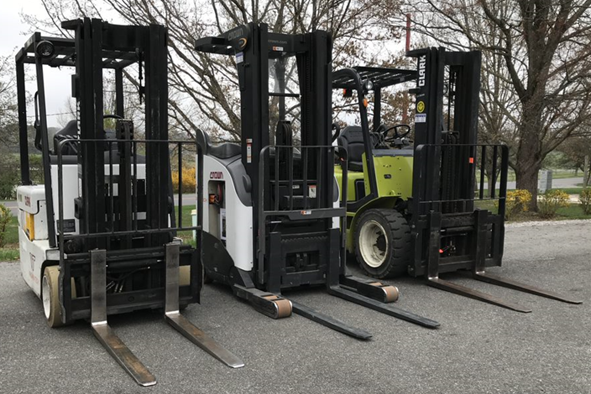
Shock impact damage is a distribution hazard that affects all pallets and unit loads, resulting in significant damages. Testing sequences have been developed to assess the resistance of pallets and unit loads to shock impact damage, and this information has been used to improve pallet design. As forklifts are widely used in the industry, common factors in these testing sequences are the simulations of forklift damage through incline impacts and free-fall drops.
The objective of this research was to investigate the effects of forklift type (Image 1), pallet design, entry speed, and top load on the horizontal shock responses. Two pallet designs were investigated during this study including a wooden and a plastic pallet design. Because the friction between the pallet and the floor could influence results, the static coefficient of friction (COF) between the bottom of the pallet and the concrete floor was measured for both pallet designs.
Two data loggers were used to measure acceleration and the horizontal shock impacts experienced during the same event on both the pallet and the forklift (Image 2). The SAVER 3X90 datalogger was mounted to the back of the fork tine carriage using Scotch permanent outdoor/exterior mounting tape. The measurements on the pallet were recorded by a SAVER 3D15 datalogger, positioned on the top lead deckboard on both pallet designs using Scotch permanent outdoor/exterior mounting tape. Data was collected from all three axial directions from both the pallet and the fork tine carriage.
Image 2. Representative picture of: (a): sensor location, and (b): sensor orientation on the forklift; (c): sensor location and orientation on the pallet.
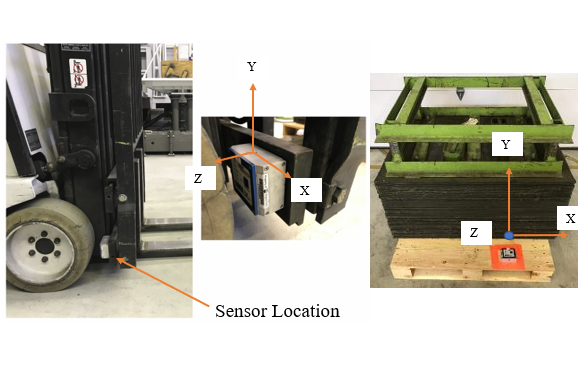
The acceleration, duration, and delta velocity responses registered for each forklift were recorded. The average acceleration measured on the forklifts was 2.98 G. The coefficient of variation obtained for these measurements was 37%, reflecting values as low as 1.38 G (for the reach truck) or as high as 5.1 G (for the gas forklift). The average event duration recorded was 13.6 ms. The coefficient of variation obtained for that event duration was 23%. While high, the variations found were considered acceptable as shock is traditionally considered a difficult parameter to characterize.
The acceleration measured in the forklifts was then used as the main response for further analysis. The p-values obtained in the analysis showed that all of the main factors (forklift type, pallet design, entry speed, and top load) significantly affect the acceleration experienced by the forklift during its interaction with the pallet. Similarly, the researchers found two-way interactions between most variables, and one three-way interaction was found to be significant as well, corresponding to the forklift, pallet design, and top load.
The measured acceleration response was significantly higher (15%) when the gas forklift was used, while the reach truck and the electric forklift were not significantly different from each other. However, event durations with the reach truck were 50% longer than with the electric forklift. When wood pallets were used for testing, the acceleration levels were significantly higher (20.7%). This result could be explained by the greater coefficient of friction between the pallet and the laboratory floor, which increased the resistance of the pallet to impact. When the impact speed was increased, the measured acceleration increased by as much as 32%, but entry speed did not affect the duration response.
The results showed that there was no significant difference in acceleration when the top load was increased from 227 kg to 680 kg. However, when the top load was further increased to 1,134 kg, the measured acceleration increased by 22%. This result indicates that, at least for heavy top loads, the weight of the top load needs to be tracked during data collection. Due to the changes in mean acceleration, pallet design and entry speed were found to be the most influential factors on the acceleration measured on the forklift at the moment of impact (Image 3).
Image 3. Interaction plot for Forklift Peak Acceleration response.
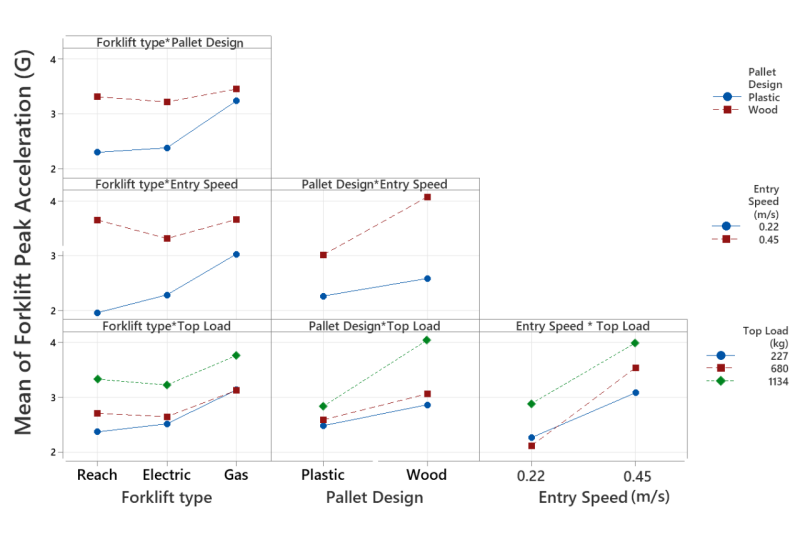
This research concluded that the intensity of the horizontal shock response exerted on the pallet varies ap-proximately 16% depending on the type of forklift used. Therefore, it is necessary to consider the type of forklift used in a warehouse when comparing acceleration intensities and their effect on your pallet durability. They also found that a plastic pallet design is associated with a 20% lower horizontal shock response in the forklift. So, caution needs to be taken during data collection in a warehouse environment because the pallet design will have a significant effect on the shock results measured. The researchers summarized that the 14% higher acceleration response that was obtained for the pallet when the speed was increased was due to increased kinetic energy during impact. An increase in the acceleration response was also found with the change in top load; however, the effect of this change was dependent on other factors such as entry speed and forklift type. The acceleration measured on the pallet is approximately 4.4 times greater than the acceleration measured on the forklift for the same impacts.