Research Highlight: Undergraduate research project testing the packaging systems of window AC units
Image 1. Vibration testing of one of the AC units
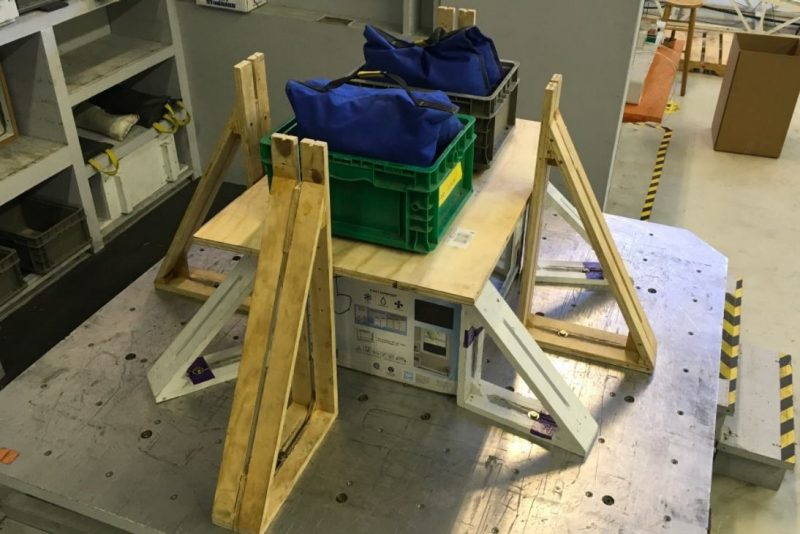
One of the largest appliance manufacturers sponsored an undergraduate research project during the 2021-2022 school year. They asked their assigned student group to investigate the packaging systems for their window AC units as compared to many of their competitor’s packaging versions. Rosa Williams (Sophomore) and Rohan Sarathy (Senior) were selected to work on the project.
Many international companies suffered from the increased supply chain costs and delays due to the COVID-19 pandemic and were forced to deal with the repercussions of the escalating US-China trade conflict; however, this project’s sponsor actually saw an increase in export sales due to the increased demand for sterilization features in home appliances such as air conditioners, humidifiers and washing machines which were already built-in features in their brand.
There were 11 different air conditioning units, each of them produced by a different company, that were sent to the testing facility. Most units were packaged into corrugated boxes and protected with molded Styrofoam cushion. Some designs had additional straps that provided added containment and one unit was secured with a stretch wrap.
The students received two packages from each AC design. The first package was used for a packaging performance evaluation using the ISTA 6 Amazon Type B testing standard. This testing sequence included a drop test, a horizontal compression test, vertical compression, four vibration sequences (Image 1), and finally a second drop sequence. Each design that completed testing underwent a thorough inspection to determine any internal damages, structural or cosmetic, to either the product or the packaging materials, that was not visible during the testing sequence. Depending on the performance throughout the testing sequence and inspection, each design was given a grade of Pass or Fail.
The second package was used to create a detailed bill of materials for each product. The goal was to understand the different packaging approaches that the different companies are employing to protect their products.
Sustainability is rapidly becoming more meaningful to consumers. In order to assess the units based on their sustainability, two ratios were used. Packaging efficiency was calculated through the ratio of product weight to packaging weight. Another ratio used the ratio of recyclable packaging materials to total packaging material weight. A sustainability score was calculated by adding these two ratios together, with higher numbers being more sustainable (Image 2). Design 5 ended up being the most sustainable package, with a sustainability score of 13.77. However, there was no relationship between the packages’ sustainability and their ability to pass the testing; all package designs ultimately failed due to vent damage and other failure modes.
Image 2. Sustainability ratios and ratings of AC packaging designs 1-11
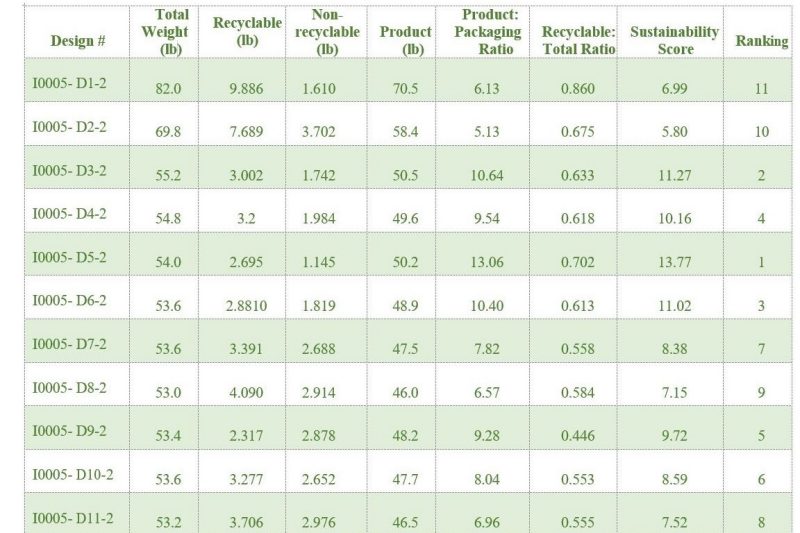
Although most of the designs failed the test, the students got valuable information on the model of failure that helped the company improve the packaging design. One of the interesting failure mode that the students observed was the failure of the tape that sealed the flaps of the package. A tape failure causes the box to lose containment and thus compromising its ability to protect the product. Amazon considers this damage as an automatic failure. Tape failure is a common failure mode during the Amazon testing thus packaging engineers are encouraged to use higher quality tape to avoid the expensive retesting cost and also damages during actual shipping.
The following semester, the students will work on redesigning the packaging system for one of the AC units with the goal to create a fully curbside recyclable packaging.