The Effect of Plastic Pails on Pallet Deflection and Pressure Distribution for Stringer Class Wooden Pallets
Image 1. Mary Paz Alvarez moving one of her unit loads of plastic pails
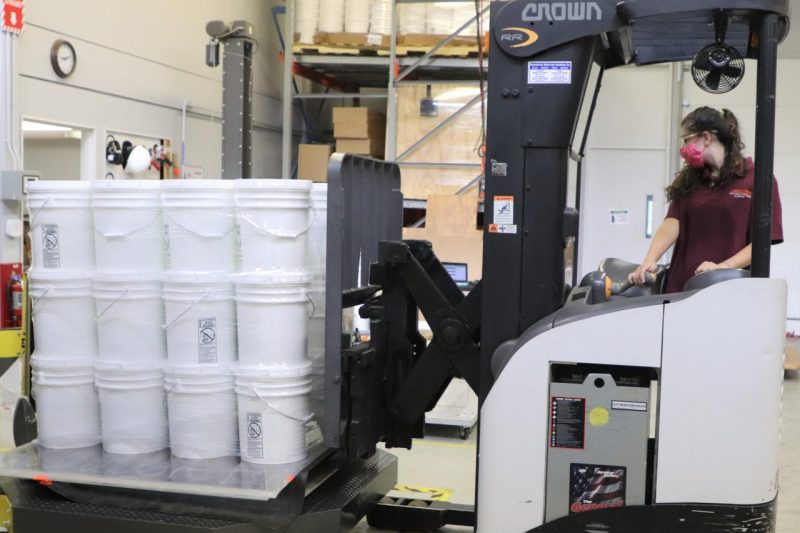
Modern-day supply chains have a great reliance on wooden pallets. Around 513 million new wooden pallets are produced annually, which are used by 94% of companies in supply chains. Most new wooden pallets are built for specific applications. The current supply chain is made up of three interacting components: products, pallets, and material handling systems. By understanding the interactions between these components, the design of each component can be optimized, and the cost and sustainability of the overall system can be improved.
Graduate student Mary Paz Alvarez has been studying the interaction effects of drums and pails on pallets’ strength and deflection levels since 2019. Her research is funded by the Pallet Foundation and the National Wooden Pallet and Container Association.
One of the ways that the supply chain components interact is called load bridging. During load bridging, the packages on top of the pallet act as discrete loads, causing the load to be unevenly distributed across the top of the pallet. Although corrugated boxes are the most ubiquitous packages in supply chains, representing 72% of products being shipped, plastic pails are also an essential packaging type.
Plastic pails are shipping containers that are used primarily to ship fluids and powders. Pails are created to be either be tight-headed or open-headed. A tight-headed pail has a nonremovable lid and is meant to be liquid tight. Open-headed pails have larger openings and a removable lid for easy emptying. Based on a survey conducted by Modern Materials Handling magazine in 2020, 7% of goods that were shipped on pallets were in plastic pails. The estimated size of the global plastic pail industry was $5.54 billion in 2019 and is estimated to increase to $6.88 billion by 2024.
The objectives of Alvarez’s research were to investigate the effects of 5-gallon plastic pails on the deflection of pallets compared to a uniformly distributed load, modeled by an airbag for testing purposes. Another objective was to investigate the pressure distribution between pallets and pails as a function of pallet design and support conditions. The most common failure mode for plastic pails is the buckling of their side walls, which can cause the pails to leak or a column of pails to become unstable and collapse. Both modes of failure can result in product damage and an unsafe work environment. In addition, pails’ circular shape might cause more concentrated pressure distributions across the top of the pallet, which could affect pallet performance.
The experimental design for this project utilized one pail design, four pallet designs, two pail stacking patterns, and four support conditions. There were three repetitions for each pallet design. The support conditions included warehouse racking across the length, warehouse racking across the width, single floor stack, and double floor stack. The greatest measured pallet deflection for each support condition was used for statistical analysis via an analysis of variance (ANOVA) test. The dependent variable was pallet deflection while the independent variables were the pallet design and the loading method.
The pressure data revealed that the load predominantly transfers to the pallet through the bottom perimeter of the pail. This is indicated by the circular distribution of the pressure. Therefore, the size of the perimeter and the design of the bottom of the pail are crucial factors that can influence the performance of the pallet. It also was observed that, due to the bending of the pallet, the entire perimeter of the bottom of the pail is not always engaged in supporting the load. The pressure tends to distribute towards the stringers parallel to the direction of pallet bending. This redistribution of pressure indicates the presence of load bridging, which explains the consistent reduction in pallet deflection when a unit load of pails is used instead of a flexible airbag.
Image 2. A) Pressure map setup for one quarter of pallet. B) Pressure map reading for plastic pails.
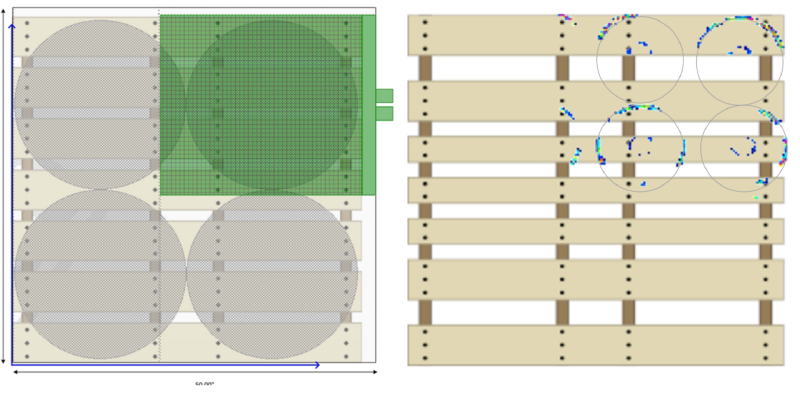
For both the warehouse racking across the length and the warehouse racking across the width support conditions, deflection decreased significantly when the pallet was loaded with pails rather than the flexible airbag. The decrease in deflection ranged from 56% to 61%. The largest reduction (61%) was found on the pallet designs with 1.27 cm top deckboard thicknesses where the pails were column stacked without nesting. The deflection of the column stacked and nested pail patterns resulted the exact same deflection for the 3-stringer pallet design with 1.27 cm top deckboards. The statistical analysis of the interaction effects revealed that the loading method has more effect on the 4-stringer and 3-stringer pallets with 1.27 cm top deckboards than for the other designs, indicating the load bridging has a greater effect on pallets with lower stiffness top decks.
Regarding the single and double stack support conditions, the ANOVA results of the single stacked support condition indicate that the pallet design and the loading method were statistically significant along with the interaction effects. Pallet deflection decreased significantly when the pallet was loaded with pails rather than the airbag. This decrease in deflection ranged from 70% to 89%. The maximum decrease in deflection (89%) was observed for the 4-stringer pallet design with 1.27 cm thick top deckboards (Table 1).
For the double stacked condition, the deflection reduction ranged from 43% to 80%. The maximum decrease in deflection (80%) was observed for the 3-stringer pallet design with 1.27 cm thick top deckboards.
When the interaction effect between the loading method and the pallet design was further investigated, the effect of pails (vs. the airbag) had the greatest change for the 3-stringer pallet with 1.27 cm top deckboards, indicating the load bridging has a greater effect on pallets with lower stiffness top decks.
Image 3. Summary table of average pallet deflections for the investigated pallet designs and loading methods in the single floor stack support condition.
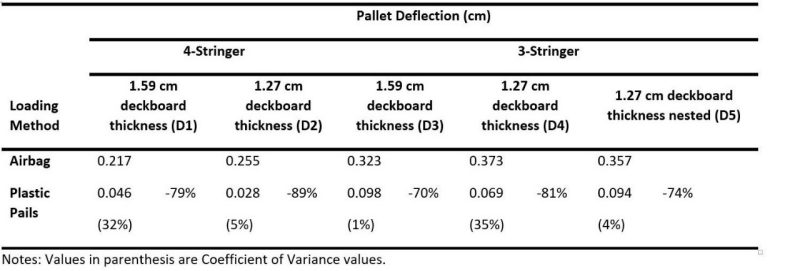
When comparing the deflections of pallet designs, similar to the warehouse rack across the width support condition, the effect of deckboard thickness was found to be significant for most scenarios. This illustrates the ongoing deflection trend by comparing the uniformly distributed load and the unit load of plastic pails while the unit loads were double stacked.
Based on her research, Alvarez has concluded that the effect of loading method was statistically significant in every support condition. Pallet deflection significantly decreases when loaded with pails compared to a flexible airbag. This reduction ranged from 32% to 89% for most pallet designs. This finding indicates that pallets supporting unit loads of pails will deflect significantly less than what they are currently designed for, and this reduced deflection could increase the load capacity of some pallet designs.
The greatest effect of the loading method was found for the single stack support condition, with 71% to 89% reduction. The load predominantly distributes down through the bottom perimeter of the pails, indicating that the size and design of the bottom of the pail could have a major effect on the load capacity of pallets. The effects of pallet design and the interactions between loading method and pallet design were statistically significant in every support condition. The effect of pallet design was proven to be important because it influenced the way pressure distributes throughout the bottom perimeter of the pail.
Overall, these results reveal that wooden pallets should be designed for the specific type of packages they will be carrying in order to optimize the cost of the pallet and reduce the amount of raw materials used to manufacture wooden pallets.
Image 5. Mary Paz Alvarez building a unit load of plastic pails.
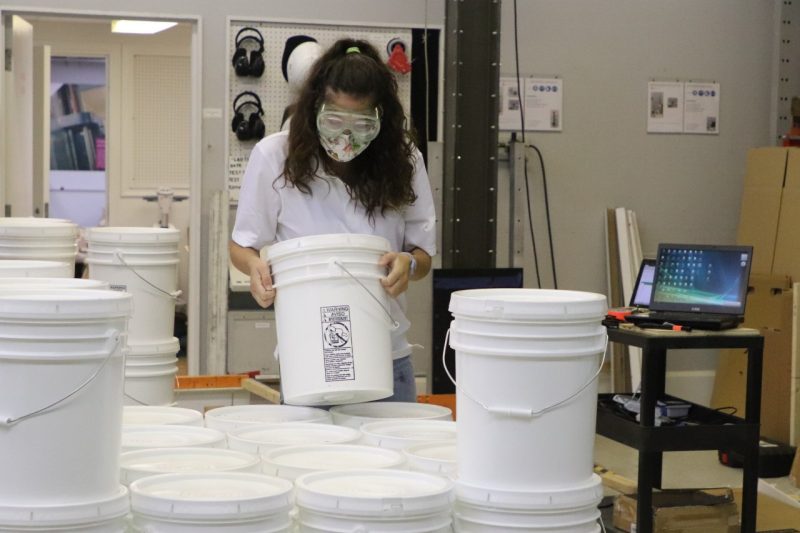