How Much Load Can My Pallet Carry?
There are many various laboratory tests and standards. Find below easy-to-follow explanations of them and how they're used to calculate the load capacity of your pallets...
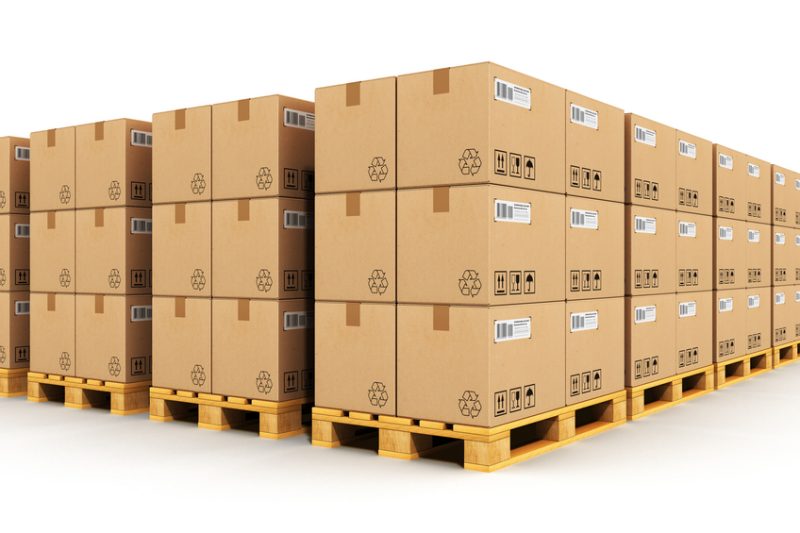
Introduction to the load carrying capacity of a pallet...
When pallets are selected for an application, a multitude of factors are considered including their size, weight, cost, load capacity, accessibility, stiffness, sanitation, etc. The “load capacity” of a pallet is the term used to describe the maximum payload that the pallet is capable of handling safely. The load capacity of a pallet is one of its most important characteristics because if the pallet cannot safely handle its payload, it cannot fulfil its fundamental purpose which is the transportation of products. However, the determination of a pallet’s load carrying capacity is not a simple task.
The load capacity of a pallet can be determined using laboratory testing or computer modeling. Laboratory tests are a simple and accurate way to measure the load capacity of a pallet. However, when there are limited sample sizes, the results obtained only provide information on the properties of the tested samples. The extrapolation of these test results to the wider pallet population requires multiple rounds of testing on many samples following national and/or international standards. Laboratory tests take time to conduct and require the manufacturing and shipment of prototype pallets to the testing laboratory.
Computer modeling is usually done on industry software that has been designed to include extensive libraries of material properties, doesn’t require specialized knowledge of modeling or mechanics, and has built in variations and safety factors to apply to your pallets’ designs. Computer modeling can help design pallets which will perform better under laboratory tests, but the laboratory tests will still need to be performed in order to certify that the pallet design meets national and/or international standards.
Laboratory Testing...
The most common standards used to measure the load capacity of pallets in the United States are ISO 8611 (Download), ASTM D1185 (Download), and AIAG RC9 (Download). Although the tests described by these standards appear to be the same, there actually are major differences between the resulting information that each of the standards’ testing provides. When the goal of using the standards is to determine the load capacity of a pallet, both support conditions and loading conditions need to be specified.
The most common support conditions include: rack support (racking load capacity), short span rack support, floor support (static load capacity), fork tine support (dynamic load capacity), conveyor support, and sling support. And, the most common loading conditions include: uniformly distributed flexible load (recommended for general purpose pallets), uniformly distributed rigid load (large boxes, bricks, flat pack furniture, etc.…), rigid line loading (specialized equipment), point loading (specialized equipment), and discrete loading by the actual product (when product is known). The following table shows the appropriate tests to be conducted in the laboratory based on the support conditions that the pallets will experience during their useful life (Table 1):
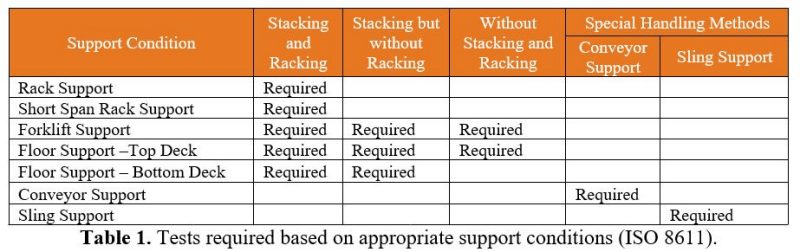
Also, when laboratory tests are being selected to measure the load capacity of a pallet, the ultimate use of the pallet in the supply chain needs to be considered.
General Purpose Pallets: These pallets are designed to be used in any supply chain while supporting any possible load for distribution. Load capacities for general purpose pallets need to be calculated using the most conservative loading conditions. This will, most commonly, mean testing using a uniformly distributed flexible load as it can be closely represented by a bladder filled with air or water. Support conditions will also need to be taken into consideration depending on the final handling of the pallet: handled using Stacking and Racking, handled using Stacking but without Racking, handled without Stacking or Racking, and special handling methods.
Special Purpose Pallets: These pallets are designed for a specific supply chain and/or for supporting a specific type of product/load. Load capacity for special purpose pallets need to be evaluated using only the support conditions that the pallet will actually encounter and using only the actual product/load that the pallet will support. It is important to remember that the load capacity generated by these tests will only apply to the exact package/load type that is used during testing. If the packaging material, pallet design, unit load arrangement, or unit load containment method changes, testing will need to be conducted again fitting the new parameters.
How to calculate load capacity?
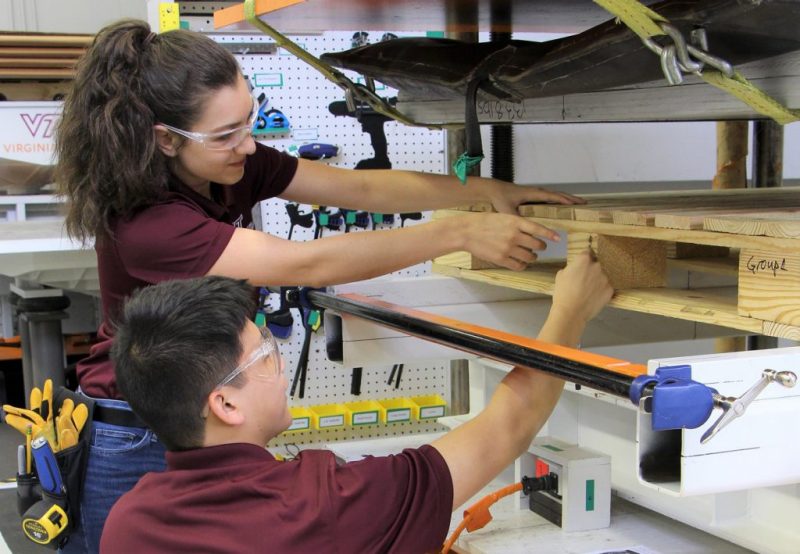
Loading and support conditions have a direct influence on the load capacity of the pallet. Once the loading and support conditions are defined, strength and stiffness tests are conducted. The load capacity of the pallet is determined by considering the results of both the strength and stiffness tests. Each of these tests, strength and stiffness, will provide a preliminary safe load. After you have found both preliminary values, the lowest of them will be the safe load capacity for the pallet in the tested support condition.
During strength tests, a pallet is loaded until the applied load results in pallet failure. This results in a finding called the “Ultimate Load” or “Failure Load.” The first preliminary safe load value is determined by dividing the ultimate load, found through the strength test, by a safety factor. This safety factor is 2 for ISO 8611 or 2.84 for ASTM D1185.
During stiffness tests, a load is placed on the pallet for a defined period of time (referred to as “creep time”) during which the deflection (bending) of the pallet is monitored. Following the creep time, the load is removed and the relaxation (unbending/straightening) of the pallet is determined after a defined period of time (referred to as “relaxation time”). The actual length of the creep time and the relaxation time are dependent upon the test standard used and the materials used to manufacture the pallets. The second preliminary safe load value is determined based on the deflection of the pallet following the stiffness test. This safe load value is the test load weight that causes the maximum allowable deflection after the defined creep time. E.g. if the pallet is allowed to deflect 0.5 in. after 2 hours, testing is done to find the load that causes the pallet to bend close to 0.5 in. at the end of the defined creep time. This is called the second preliminary safe load of the pallet.
The lowest of the two preliminary safe load value will be the safe load value for the tested support condition.
It is important to realize that even if two pallet designs have the same ultimate/failure load (from their strength tests), they can end up with two completely different load capacity ratings depending on their stiffness and time dependent (creep) behavior. However, for high stiffness pallets, such as wood and metal, their time dependent behavior might not be as important because their load capacity will mainly depend on the results of the ultimate load (strength) tests. This is because high stiffness pallets do not deflect enough for their deflection be limiting to their load capacity.
Conversely, for low stiffness pallets, such as plastic or corrugated, the load capacity will depend more on the stiffness tests (the time dependent [creep] behavior) then on the ultimate load findings (strength tests). If the time dependent behavior of two pallets are similar, then the stiffness of the pallets will become the major factor determining the load capacity. For example, take two pallets with the same ultimate load capacity and the same time dependent behavior, but they are of different stiffnesses - the lower stiffness pallet will receive a lower load capacity rating despite the other factors being the same as the higher stiffness pallet.
However, if the time dependent behavior of the two pallets is different, both the stiffness and the time dependent behavior will need to be considered. If you have two pallets with the same ultimate load capacity, but the time dependent (creep) behavior of pallet A is much greater than pallet B then, even if pallet A has greater stiffness, pallet B might receive a greater load capacity.
Load Capacity Values from Different Tests...
When selecting a pallet design, it is essential to compare the safe load values that are found through the various tests to each other. One of the potential issues encountered during laboratory tests include the fact that none of the current standards define whether to use the average safe load found though the tests or to use the minimum safe load found through the tests. This causes major difference between the results provided by different laboratories. Another possible issue is that the number of pallet samples required to be tested by the standards generally isn’t enough to be representative of all pallets. The following sections provide detailed explanations of the results provided by the different laboratory tests.
Bending Test Using Warehouse Racking Support (Racking Capacity)
This test provides information on the load capacity of a pallet which is being supported in a free span rack system such as a load beam rack, a drive-in rack, or a drive-through rack. If the pallet is reinforced with wire
decking or additional support beams, then this test will significantly underestimate the pallet’s load capacity. During this test, the pallet is supported by two, 2 in., parallel support beams. The load capacity provided by this racking test is called the Rack Capacity. The deflection under the test load following the creep test is limited to 1.9% (ASTM D1185) or 2% (ISO 8611) of the distance between the supports. E.g. a 48 in. x 40 in. pallet supported on two 2 in. beams that are 36 in. apart is only allowed to deflect (bend) 0.68 in. (ASTM D1185) or 0.72 in. (ISO 8611) during the stiffness test.
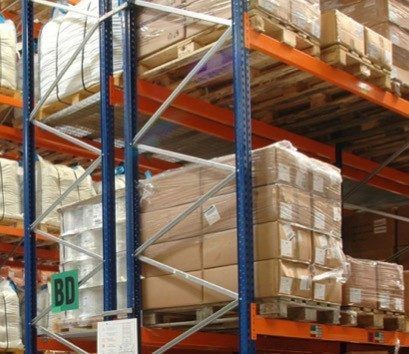
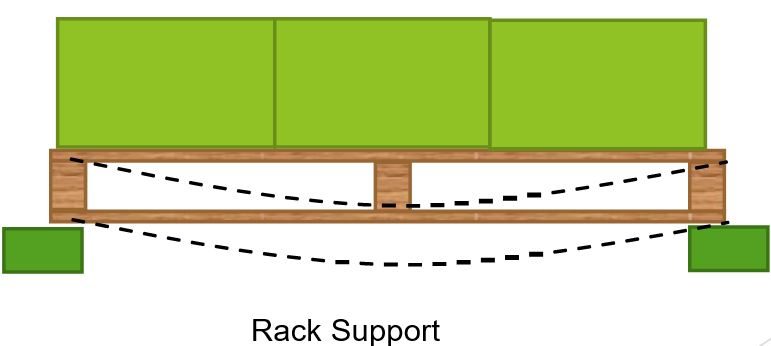
Bending Test Using a Short Span Rack or Conveyor Support
Only ISO 8611 has a test simulating a conveyor or short span rack support. This test is referred to as a Bottom Deck Bending Test (ISO Test 5). This test simulates a flow rack support with spans short enough that the support beams end up under the bottom deckboards. During this test, the load is applied to the bottom deckboards by two, 2 in., rigid load beams. The deflection of the pallet under load cannot exceed 0.6 in. (ISO 8611).
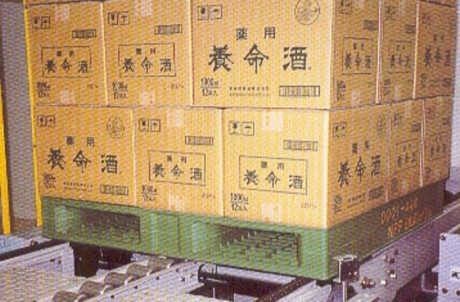
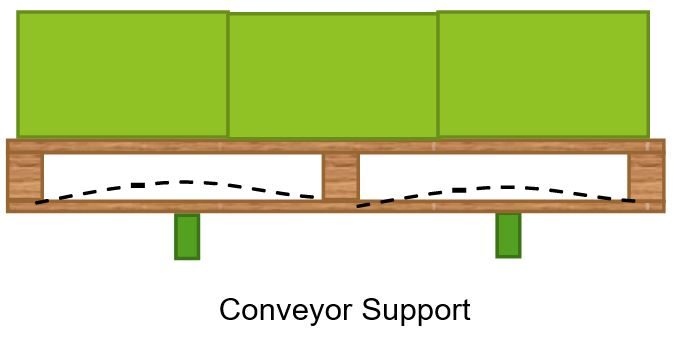
Bending Test Using Forktine Support (Dynamic Capacity)
This test provides information on the load capacity of a pallet that is supported by 4 in. fork tines positioned either half way between the blocks or stringers (ASTM D1185) or a specific distance from each other (ISO 8611, AIAG RC9). The assumption for these tests is that the fork tines are long enough to support the whole pallet. The load capacity provided by this test is called the Dynamic Capacity. The deflection under the test load following the creep time is limited to 1.9% (ASTM D1185) or 2% (ISO 8611) of the distance between the supports.
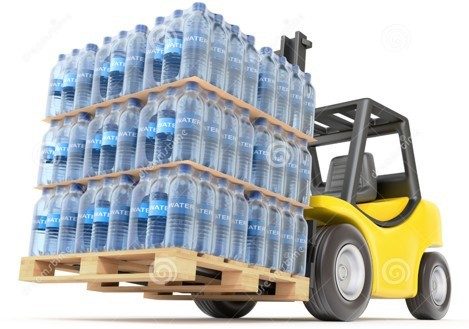
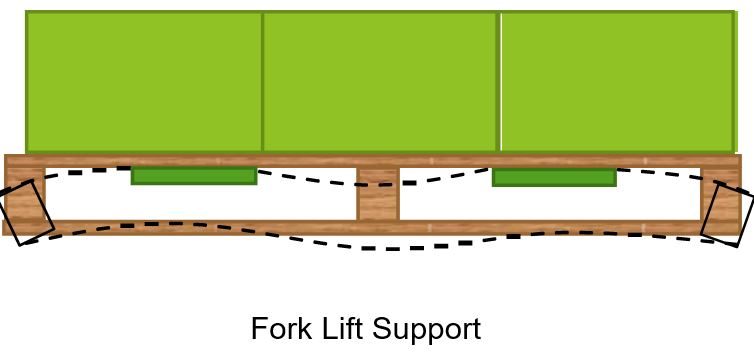
Compression Test Of Blocks Or Stringers (Static Capacity)
A compression test of blocks or stringers provides information on the load capacity of the pallet while supporting a flat, rigid load. Examples include ready to assemble furniture in boxes, metal coils, or bundled metal sheets – any packages that cover a full cross section of the pallet. The assumption for this type of loading condition is that the product fully bridges the pallets’ supports. The load capacity of pallets during this type of test mainly depends on the strength and stiffness of the pallets’ blocks and stringers. For a 48 in. x 40 in., two-way, stringer pallet with five 3.5 in. top deckboards and 1.5 in. wide Red Oak stringers, this value could be as much as 27,000 lbs. For some reinforced composite pallets, it could be as much as 60,000 lbs. It is important to remember that this value, the static capacity of the blocks or stringers, is not the same as the static capacity of the pallet which is discussed in the next section. These two static capacity values are not interchangeable. The deflection of the pallet under this load and test cannot exceed 0.16 in. (ISO 8611 and ASTM D1185).
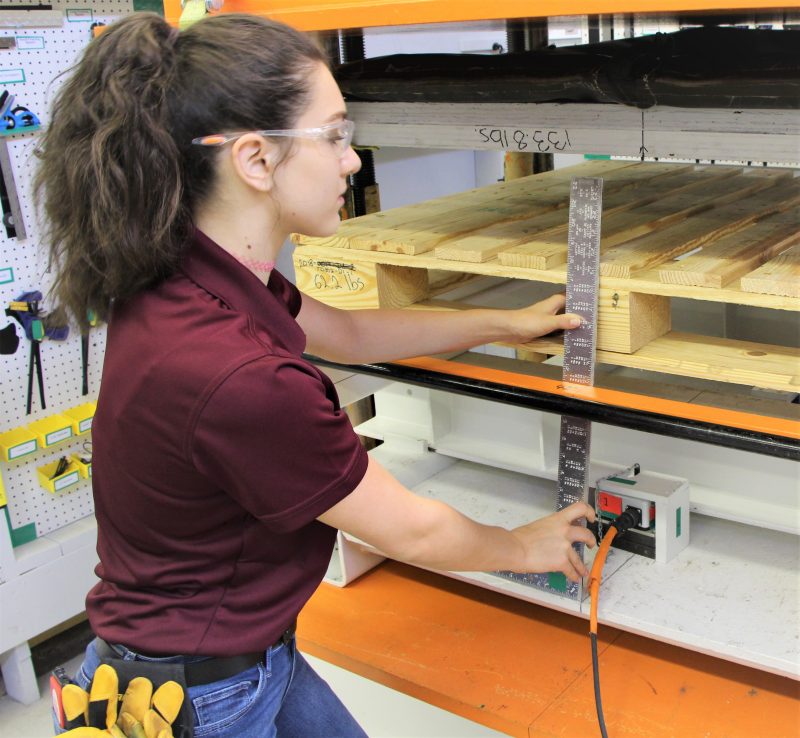
Top & Bottom Deck Bending Test Using Floor Support (Static Capacity)
The process for finding a pallet’s Static Capacity is divided into two separate tests: a top deck bending test and a bottom deck bending test. During these tests, one side of the pallet is fully supported while the other side is loaded with a test load. This test load will cause the pallets’ top or bottom deckboards to bend. The top deck test simulates the load on the top of a bottom pallet in a stack. The bottom deck test simulates the load on the bottom of the second pallet in a stack. The clearance between the top and bottom deck is important for handling throughout distribution; this clearance is what may change due to a pallet’s deflection during these tests. The load capacity provided by these top and bottom deck bending tests is referred to as the pallet’s Static Capacity. The deflection under the test load following the creep test is limited to 1.5% (ASTM D1185) to 2% (ISO 8611) of the distance between the pallet blocks or stringers. In addition to making sure that the deflection limit is not exceeded, it is also important to make sure that there is still enough clearance between the top and the bottom deckboards while under load for a pallet jack’s fork tines. The most common tine thickness on pallet jacks is 3.25 in. It is also important not to mix this result with the Bottom Deck Bending results (ISO 8611 Test 5). That test actually simulates support by a twin track conveyor or short span rack system.
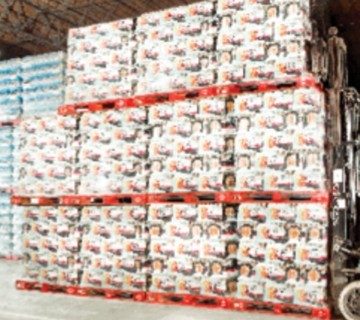
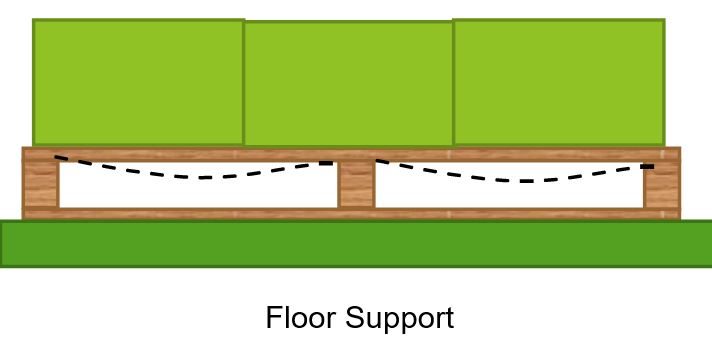
Computer Modeling...
Computer modeling can be done with finite element modeling or with specific wood pallet design software such as:
- The "Pallet Design System" by the National Wood Pallet and Container Association
- "Best Pallet" & "Best Load" by White and Company
These softwares can only be used for designing wood pallets and include an extensive library of material properties. Using a software means you don't need to have an extensive knowledge of modeling or mechanics to design a usable pallet. Softwares come with built in variation and safety factors so even a novice designer can develop a strong, stiff pallet. There are many different types of load analysis that can be conducted with pallet designing softwares - such as the measurement of the distribution of pallet strength, the payload distribution, and the ultimate load.
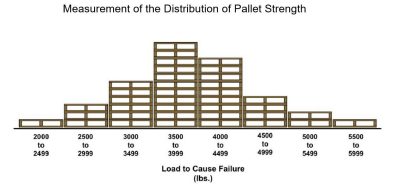
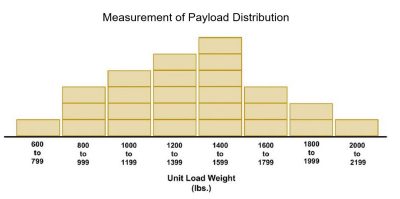
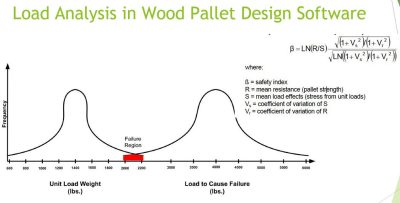
Computer modeling can be done with finite element modeling as well. This is used primarily for designing plastic pallets. It is much more time consuming of a process and it's accuracy depends on the material properties entered and the support conditions used.
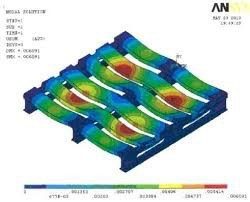
Recently, many studies have focused on the effect that packages have on pallets. The various sizes and shapes of packages may add to or take away from the stiffness of the pallet they're shipped on - hence increasing or decreasing the pallets' deflection, strength, and ultimate load.
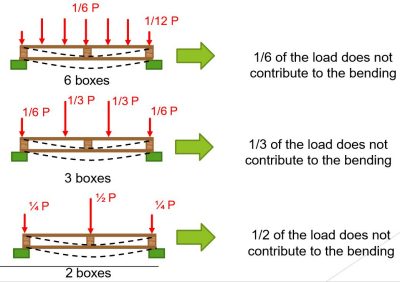
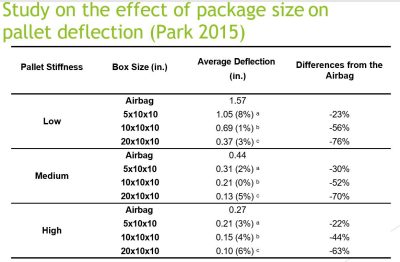
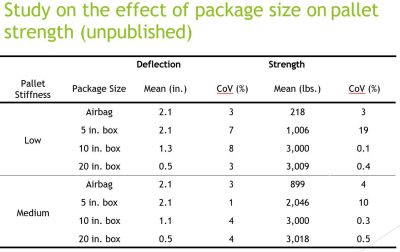
Differences Between Testing Standards...
ASTM D1185 (2009)
“ASTM D1185 – Standard Test Methods for Pallets and Related Structures Employed in Materials Handling and Shipping” is distributed by ASTM International. This standard differentiates between General Purpose and Special Purpose pallets. This standard is generally accepted in the United States. For general purpose pallets, the load needs to be applied using a flexible airbag. Only a two-hour, creep test is required by this standard. The racking spans are 2 in. greater than ISO 8611 requires, and the deflection limit is slightly more conservative (1.9% or 1.5% instead of 2% for ISO 8611). For special purpose pallets, both strength and stiffness tests need to be conducted using the actual product that the pallet is designed to carry. The ASTM D1185 standard recommends testing a minimum of three sample pallets. Acceptable loading conditions for this standard are (1) representative loads (case goods, bagged goods, blocks, barrels, etc.), (2) a flexible airbag, or (3) concentrated loads. ASTM D1185 is the oldest general pallet testing standard.
ISO 8611
“ISO 8611 – Pallets for Materials Handling – Flat Pallets” is distributed by ISO (International Organization for Standardization). This standard is composed of three parts. Part 1 contains test methods, part 2 contains performance requirements, and part 3 contains information about the maximum working load tests. ISO 8611 is one of the newest general pallet testing standards, and it is accepted internationally. ISO 8611 differentiates between nominal loads and maximum working loads. Nominal loads are the lowest safe load value for the specified support condition, independent of the type of load (though it does exclude concentrated loads). A maximum working load is the load that a pallet can safely carry under specific loading and support conditions. Maximum working load tests are generally conducted with the pallet is only designed to transport a specific type of product or package. The nominal load test is similar to the ASTM D1185 test that is conducted with a flexible airbag. Meanwhile, the maximum working load test is similar to the ASTM D1185 test that is conducted with a representative load.
It is important to note that these two tests provide completely different results which should must be interpreted differently. The results of the nominal load test are applicable to a wide range of products, but the results of the maximum working load test are only applicable to the specific type of unit load that was evaluated. Thus, any changes to containment force, method of containment, size of packages, number of layers, or type of packages makes the maximum load test results invalid, and requires that the tests be redone.
For the nominal load test, ISO 8611 requires the use of rigid load applicators. The locations where the load applicators are placed are decided upon in order to closely simulate the bending of a pallet that is loaded with a uniformly distributed load (ASTM tests this with the flexible airbag). However, for some pallets, the difference between airbag loading and rigid bar loading is significant. Although it is not explicitly stated in the standard, it is important to mention that if the pallet breaks around the load applicators, then the test is invalid. ISO requires longer creep tests for pallets made from plastic materials (24 or 48 hours) than ASTM D1185. Also, ISO, has different spans for many tests, and allows slightly larger deflections.
AIAG RC9
“AIAG RC9 – Container Performance Test Guidelines – 3rd Edition” is published by the Automotive Industry Action Group (AIAG). The standard is designed to provide comparative test procedures for small containers, large bulk containers, and pallets used in the U.S. automotive industry. The goal of this standard is “to provide a common methodology by which containers can be compared on an objective one-to-one basis” (AIAG RC9 ed. 3). This standard does not provide estimates of the load capacity of the pallets – it only offers comparative analysis as it does not have realistic loading conditions. The tests contained in this standard are as follows: forklift deflection test, rack deflection test, compression test, leg strength test.
Pallet Specifications for Automated Warehouses...
Automated warehouses are a growing trend in the U.S. However, these highly efficient, high-speed facilities pose new challenges for pallet designers. Cycle time and speed of operations have the utmost importance; thus, pallet designers need to make sure that their pallets do not cause bottle necks in the automated systems.
In 1997, Material Handling Industries of America funded a study to investigate the challenges posed by automated warehouses on pallet design. The outcome of this study was published in Chapter 10 of the 2016 version of the American National Standards Institute (ANSI) MH1 standard. Because automatic systems are highly sensitive to any variations, pallet quality and pallet stiffness have become even more important. The allowable size variations and deflections of pallets are limited by the clearance between the warehouses’ equipment and pallets. An analysis of clearances revealed that the maximum allowable deflection for a pallet under load is 0.5 in., while the maximum allowable deflection for pallet components under load is 0.25 in.
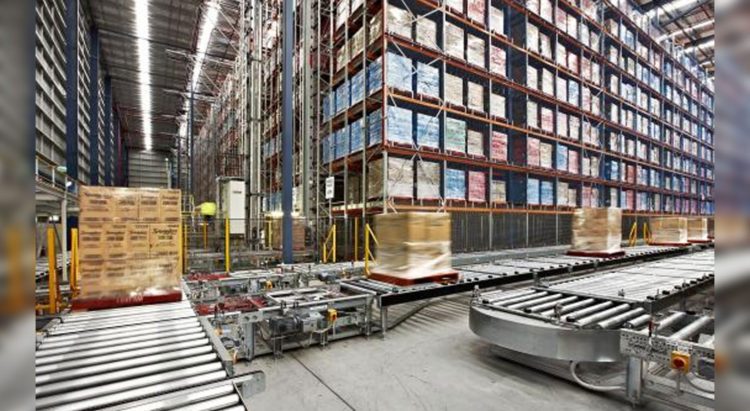
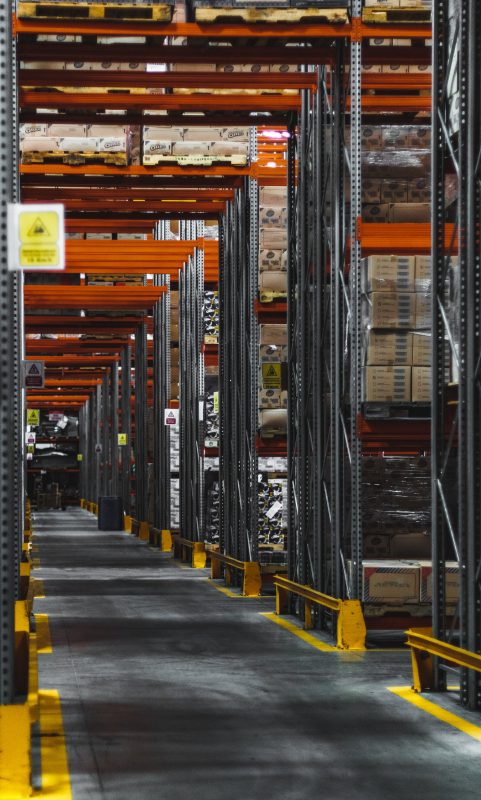
Big Box Stores Pallet Requirements...
Many of the large retailers have specific requirements for any subcontractor wishing to sell through their stores. Some of the current big box store requirements are:
BJ’s Wholesale: Each pallet must be capable of supporting its own weight to allow double-stacking. A typical pallet build would be 47” high (including the pallet) with a maximum weight no more than 2500 pounds (though this can vary based on product categories and merchandising methods). The purchase order and/or BJ’s Buyer will determine the specific pallet configuration and pallet height for each product. (2013 Packaging Spec).
Walmart: Walmart requires that all pallets shipped into Walmart DCs meet or exceed the Grocery Manufacturers Association (GMA) Grade “A” pallet standards. Product may be stored in a standard rack on a supplier’s pallet for an extended period of time. Pallets must support the weight of the product shipped on them.
Costco: If pallets will be manufactured by different companies, or using different materials at different times, each unique pallet must be represented by its own PDSTM Report, and each Report must be approved. (2011 Pallet Spec).
Conclusions:
- To measure the correct load capacity of a pallet, the appropriate loading and support conditions need to be determined.
- The load capacity of pallets is highly dependent on the combination of their ultimate load, stiffness, and time dependent behavior.
- The load capacity of pallets can be determined using either laboratory testing or computer modeling.
- There are three major laboratory testing standards commonly used by the industry: ASTM D1185, ISO 8611, and AIAG RC9. There are major differences between these laboratory testing standards in scope and also in the load capacity values that they provide.
- Computer modeling is an effective way to get load capacity values; however, physical tests are always need to be conducted to verify the predicted values.
- The load capacity of pallet highly dependent on the properties of the payload supported by the pallet.
- The deflection of the pallet is limited in automated warehouses which put a constraint on pallet design.
References:
ASTM International. (2017). Standard Test Methods for Pallets and Related Structures Employed in Materials Handling and Shipping (ASTM Standard No. D1185-98a(2017)). Retrieved from https://www.astm.org/Standards/D1185.htm
Automotive Industry Action Group. (2015). Container Test Performance Guidelines (AIAG Standard No. RC9, 3rd edition). Retrieved from https://www.aiag.org/store/publications/details?ProductCode=RC-9
Horvath, L. (2019, October 8). How Much Load Can My Pallet Carry? [Webinar]. In Center for Packaging and Unit Load Design’s 2019 Industry Webinar Series. Retrieved from www.unitload.vt.edu
International Organization for Standardization. (2011). Pallets for Materials Handling – Flat Pallets – Part 1: Test Methods (ISO/DIS Standard No. 8611-1:2011). Retrieved from https://www.iso.org/standard/50114.html
International Organization for Standardization. (2011). Pallets for Materials Handling – Flat Pallets – Part 2: Performance Requirements and Selection of Tests (ISO/DIS Standard No. 8611-2:2011). Retrieved from https://www.iso.org/standard/50115.html
International Organization for Standardization. (2011). Pallets for Materials Handling – Flat Pallets – Part 3: Maximum Working Loads (ISO/DIS Standard No. 8611-3:2011). Retrieved from https://www.iso.org/standard/50116.html