Research Highlight: Investigating the effect of pallet top deck board stiffness on corrugated box compression strength as a function of several variable factors
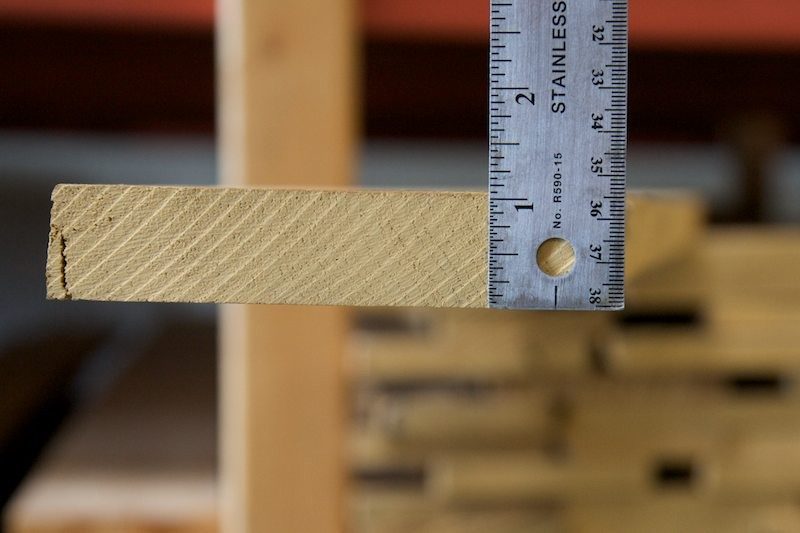
Historically, the distribution packaging industry has adapted the method of unitizing single, multiple, or bulk products on a solid platform in order to ease handling, storing, and transporting. Unit loads dominate today’s product distribution and storage format in the United States by 80%, and most of these unit loads are carried on pallets. Just as pallets have become one of the essential elements of a unit load, corrugated boxes also play a crucial role in the unit load system. Corrugated boxes are the most used type of primary and secondary packaging; in fact, 72% of pallet loads consist of stacked corrugated boxes. When designing a unit load, accurately predicting corrugated box compression strength is crucial to avoid package failure from vertical compression. Numerous studies have investigated the factors that affect the compression strength of corrugated boxes, including material properties, manufacturing methods, and environmental condition factors.
In recent years, researchers have endeavored to correlate the effect of pallet top deck stiffness (Image 1) to corrugated box compression strength. Researcher Quesenberry found that a stiffer top deck board could increase the compression strength of asymmetrically supported corrugated boxes up to 37% when the unit loads are double stacked on the floor. He also discovered that the effect of pallet top deck stiffness on box compression strength could be utilized to lower the cost of a unit load by decreasing the required board grade of corrugated boxes and increasing the top deck thickness. Their experimental unit load designs were enough to see the trend of this phenomenon, yet a limited number of designs for understanding other factors that may affect the result. Therefore, this current research project investigated the interaction between pallet top deck stiffness and box compression strength as a function of variable factors such as starting top deck thickness, pallet wood species, box size, and board grade, in order to suggest an effective way of applying the unit load optimization method.
This study consisted of two main sections: validation of the analytical pallet design software, and unit load scenario analysis. The commercially available pallet design software Pallet Design System™ (PDS™), created by NWPCA, was utilized to replace numerous physical experiments in this study. The box performance data predicted from PDS™ and Quesenberry were compared using the Pearson correlation coefficient.
After the software validation process, a total of 288 unit load scenarios were simulated using PDS™ for unit load analysis to investigate the effect of four variable factors. The pallet designs for these unit load scenarios were varied by four initial top deck thicknesses and four wood species. The corrugated box designs were altered by three box sizes, two flute sizes, and three ranges of board grade reduction for each flute size. Finally there were three unit load configurations (Image 2).
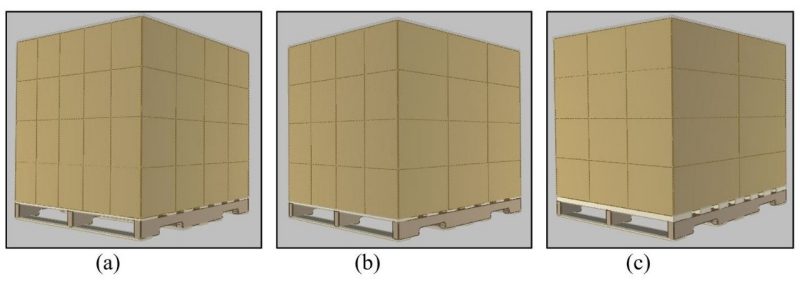
The concept of a unit load cost optimization method that allows for the use of corrugated boxes with decreased board grade by increasing the pallet’s top deck thickness was adopted from Quesenberry as a way of modifying each unit load scenario. In other words, the analysis was done by determining how much the top deck thickness needed to increase in order to lower the board grade by one level from the initial unit load scenario’s specific deck board thickness and board grade. Finally, the amount that the top deck thickness increased was color-coded into one of three grades for better visualization and identification of the level of top deck thickness increase: green for less than 0.5 in. increase, yellow for 0.5 in. to 1 in. increase, and red for beyond 1 in. increase. Figure 2, below, displays changes in the proportions of the differently colored scenarios as a function of investigated variable factors.
- Initial top deck thickness effect (Image 3A): It was observed that as the initial top deck thickness increased, there were significant reductions in the proportions of green scenarios. Correlatingly, a considerable increase in the ratio of the red scenarios was found as the initial top deck thickness increased. This result revealed that when the boxes are shipped on pallets with thinner top deck thickness, increasing the the thickness of the top deckboard could be justified by the cost savings achieved by the reduction of the corrugated box board grade.
- Wood species effect (Image 3B): It was found that, as the lower stiffness wood species are used for pallet material, a larger number of them fell under green scenarios than the scenarios built with relatively stiffer species. This result indicates that pallets built with lower stiffness wood such as low-density green wood tends to have more opportunities to reduce the packaging cost by utilizing the effect of top deck stiffness on box compression strength. The optimization of pallets made of KD Souther Yellow Pine tends to be less feasible due to the stiffness of the material and also the limited deckboard thickness options available.
- Board grade range effect (Image 3C): It was discovered that as the difference in ECT levels between the two consecutive board grades increases, the proportion of green scenarios significantly drops, and the ratio of red scenarios increases. These results also indicate that the higher the initial board grade is, the more opportunities there are to reduce the board material with minor top deck thickness, mostly due to the heavier weight of the higher board grade boxes which will bend the pallet more initially. The higher initial board grade denotes a heavier unit load which bends the pallet more, leading to the same effect as a lower stiffness pallet.
- Box size effect (Image 3D): Finally, it was observed that as the packaging size increased, the ratio of green scenarios gradually decreased whiles the proportion of red scenarios increased. These results suggest that unit loads built with small-sized boxes will have more opportunities to experience significant changes from the effects of the top deck stiffness on the compression strength of asymmetrically supported boxes than unit loads consisting of larger boxes due to the lighter weight of the unit loads with larger-sized boxes.
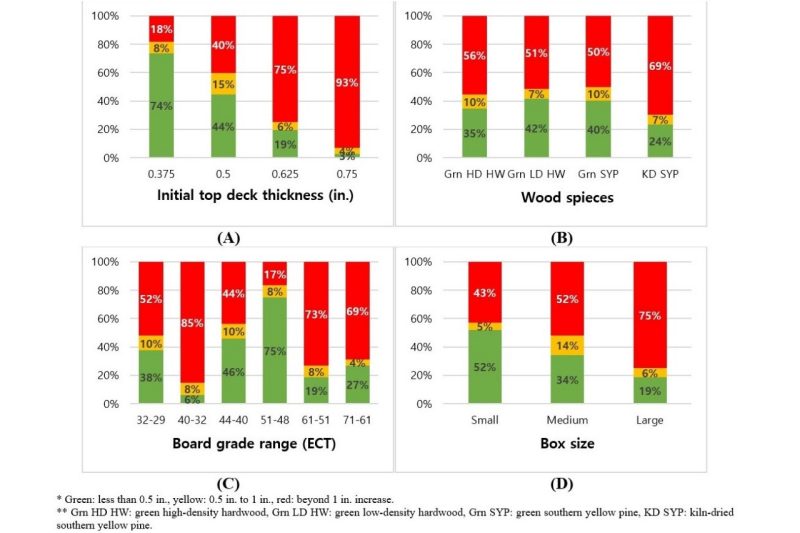
Conclusions:
The main conclusions of this study were as follows:
- The benefit of increasing a pallet’s top deck thickness in order to reduce the corrugated board grade diminishes as the initial top deck thickness increases.
- The benefits of increasing the top deck thickness diminishes as stiffer wood species are used to build a pallet. The number of opportunities to improve unit load design was similar among the three green species, but it significantly declined when KD SYP was used.
- The effects were more conspicuous when the initial pallet was very weak, which meant that improved pallet quality and decreased unit load cost could be achieved using this approach.
- There were more possibilities of decreasing board grade when initial board grade variation was lower, or the initial board grade was higher mostly due to the heavier weight of the higher board grade boxes which will bend the pallet more initially.
- The benefits of increasing the top deck thickness decrease as larger-sized boxes were used due to the lighter weight of the unit loads with larger-sized boxes.
- The effects were more pronounced when the unit load had initially been designed with a heavier top load due to more severe initial pallet bending.
In conclusion, supposing that a company already uses unit loads consisting of lower stiffness pallets or small-sized, high-grade board, corrugated boxes, this study suggested that increasing top deck thickness and reducing board grade will provide extra cost-benefits and better pallet quality. The next phase of this project will focus on characterizing the environmental impact of the effect of increasing pallet top deck stiffness on box compression strength.