Research Highlight: Analysis of the deck board stiffness effect and the location effect on unit loads of plastic pails on wooden pallets
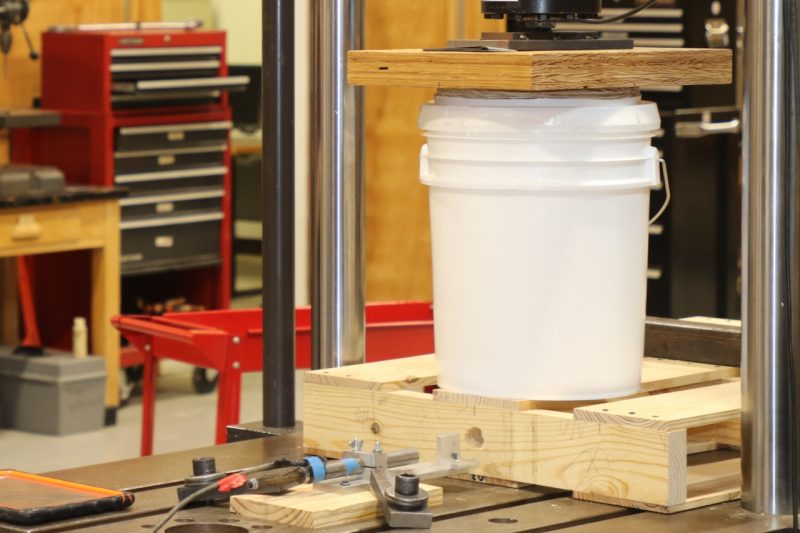
The supply chain is composed of three physical components: packages, transportation, and pallets. In order to efficiently design unit loads, it is integral to understand the interactions between these components. Previous studies have been done looking at how corrugated boxes interact with pallets throughout the supply chain. Flutes, box sizes, stacking patterns, and unit load containment have all been previously studied for corrugated boxes.
However, plastic pails are a different type of package that is mainly used to ship liquids and powders. The most common pail size is 5-gallons. Plastic pails are different than corrugated boxes in their geometry, materials, and stacking patterns. There is a lack of information about pails; unit load designers are unaware of how the plastic pails will interact with the same pallets that corrugated boxes are shipped with. The Center for Packaging and Unit Load Design conducted a previous study on unitized pails, but at that time, did not investigate the effect of plastic pail placement or how it relates to the deck board stiffness effect.
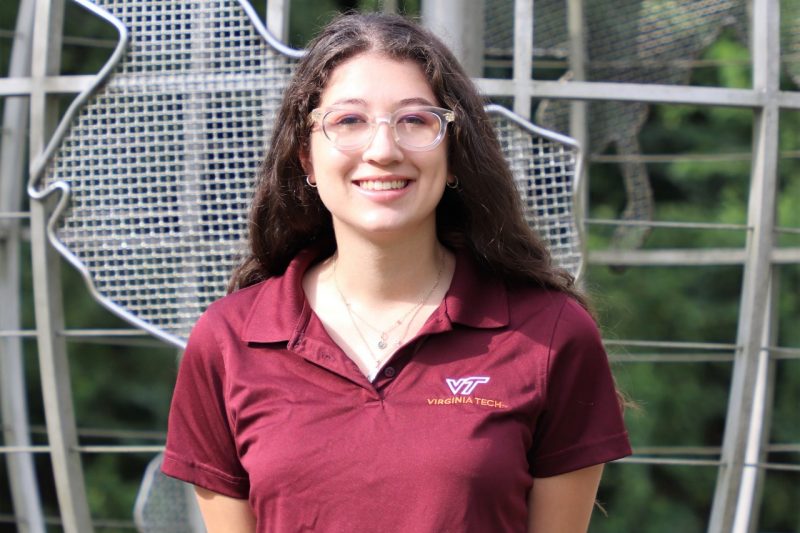
Mary Paz Alvarez, a Ph.D. student with CPULD (Image 2), is funded by the Pallet Foundation and the National Wooden Pallet and Container Association (NWPCA), and she has begun a new research project. Understanding how plastic pails interact with pallets will be useful information for designers, as they can use the info to design safer, more cost effective, sustainable unit loads. With that in mind, the objectives of this study were first to understand how pallets’ deckboard stiffness affects the failure of unit loads of plastic pails. Second, they investigated how the amount of overhang of the plastic pails could affect the failure of unit loads of plastic pails.
The pails utilized in this study were 5-gallon open headed plastic pails. The test was conducted in an MTS machine which used a 5,000 lb. load cell to measure the amount of load forced onto the pail before it failed. Failure load was determined as being the highest amount of load that the plastic pail could handle before buckling; hence, no longer being able to handle any further increase in load.
The plastic pails were tested on a “small-scale pallet segment” that was composed of three stringers and two deck boards that had varying thicknesses of 0.375 in., 0.5 in., 0.625 in., and 0.75 in. Deck boards were placed on the stringers in such a way as to create gaps. The plastic pail location was investigated first in order to understand which locations presented the best- and worst-case scenarios for the plastic pail. They were tested in five locations; centered on the pallet, centered between stringers, on the edge of the pallet, 1.5 in. offset from the center stringer, and 2.6875 in. offset from the center stringer (Image 3). Five replicates were conducted for each location. Once the best and worst location were determined, which was the center of the entire pallet and the edge, an additional 5 replicates were conducted using the four different deck board thicknesses. An ANOVA analysis was also conducted using the failure mode data from testing.
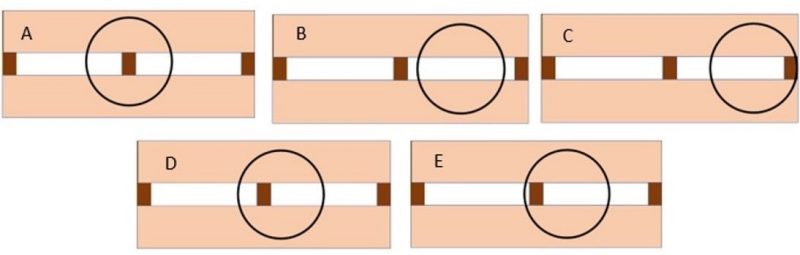
The results indicate that the largest difference between locations was seen between the plastic pail that was centered on the pallet and the plastic pail placed on the edge of the pallet. This is due to the difference in where the load is being transferred. When the pail is in the center, the pressure from loading is distributed evenly on the pallet’s center stringer while the pail on the edge is forced to unevenly distribute the force onto the end stringer on which it rests. The more symmetrically a pail can distribute its pressure, the higher the failure load (Table 1).
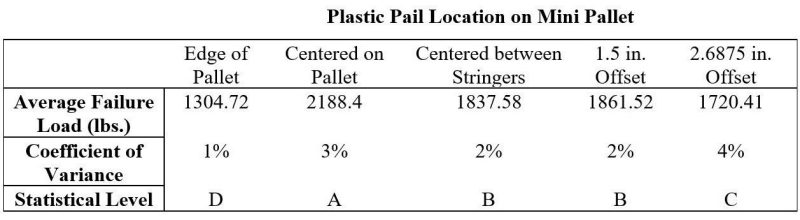
Once the best- and worst-case locations were determined, both locations were tested with all four pallet deckboard thicknesses. When analysis was conducted, it was found that the location of the pail, the thickness of the deck board, and the interaction between the two were all statistically significant. Also, the effects of the varying thicknesses of the pallet deck boards were all statistically different, but the 0.625 in. and 0.5 in. thicknesses produced similar average failure loads. When the pails are supported around the edge of the pallet, the effect of deckboard stiffness is more prominent, causing a 32% reduction compared to the 15% reduction when the pails were supported around the center for the pallet. The failure loads of each location illustrate a trend where the stiffer the deck board, the more load that the pail can receive before failing (Table 2 and Table 3).
Based off of the sets of experiments that were conducted for this research project, the conclusions that have been determined revolving around plastic pail performance on mini pallets are as follows:
- The location of the pail on the pallet has significant effect on the pail strength. This phenomenon could be explained with the asymmetric load distribution observed when one edge of the pail was supported on the stringer of the pallet. The finding is similar to what was observed for corrugated boxes.
- Deck board thickness is statistically significant and can affect the performance of a plastic pail. However, the magnitude of the effect is more pronounced when the pail is asymmetrically supported around the edge of the pallet.
The results of the experiment indicate that unit load designers can incorporate the concepts of pail placement and pallet deckboard thickness into the unit load design process. This will help designers use the stiffness of pallet top deck to reduce the amount of plastic used for pails.