Evaluation of Pallet Deflection Under Forklift Handling Conditions
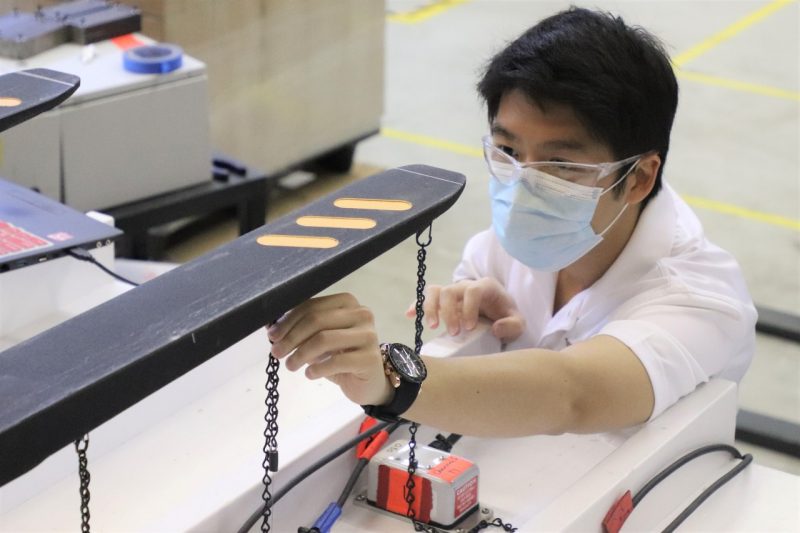
Industrial forklifts are one of the most common types of handling equipment for unit loads in warehouses and distribution centers. When unit loads are transported, the vibration caused by the different transportation modes has a major effect on the damage caused to the products transported. Therefore, vibrations caused by different common transportation modes is well-characterized. However, despite the popularity of the forklift, only a limited number of studies have researched the vibrations caused by them.
Pallets deflect while being transported by forklifts. This is caused by the weight of the unit load, with most of the deflection occurring on the outside edges and corners of the pallet. Limits for the allowed deflection of a pallet during forklift handling can be found in many international standards. However, there is still a lack of understanding about how the maximum allowed bending of the pallet influences the safety and performance of the pallet during forklift handling. Understanding pallet bending during dynamic forklift movement and how it affects the stability of a unit load will help improve the industry testing standards, and will help engineers design safer and more cost-effective pallets.
The goal of this study was to evaluate pallet deflection during static and dynamic environments, and investigate how these values are affected by factors such as fork tine orientation (level or 4° angle), unit load condition (bound or unbound), pallet orientation (across width or across length), and type of forklift handling condition (static or dynamic). Master’s student Yu Yang Huang conducted this research, which was funded by the CPULD Industrial Affiliate Membership (Image 2).
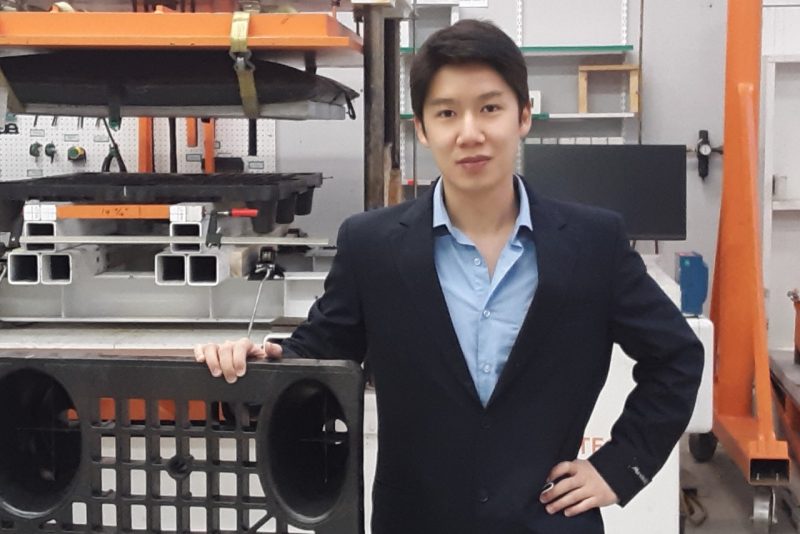
One plastic pallet design was used to conduct the experiments in this study. The pallet was a 48 in. x 40 in. nestable, block class, non-reversible, plastic pallet used for grocery distribution. Regular slotted container-style corrugated boxes were used. The boxes were manufactured with a Kongsberg computerized cutting table; constructed using C-Flute, single-wall, corrugated board with 32 lb./in. nominal Edge Crush Test value; and had external dimensions of 8 in. x 8 in. x 10 in. to create the most conservative setup. This study was conducted using both a stretch wrapped (bound) and an unwrapped (unbound) unit load. Both unit loads were constructed four layers tall, in a column stacked pattern, with thirty boxes per layer.
The coefficient of friction (CoF) of the pallet was determined for each of the pallets. The pallet was exposed to the test surface (corrugated), and a horizontal force was applied to the pallet at a constant rate of 1.0 in. / minute. Force was applied until motion was achieved and that force was recorded as Fh (Image 3).
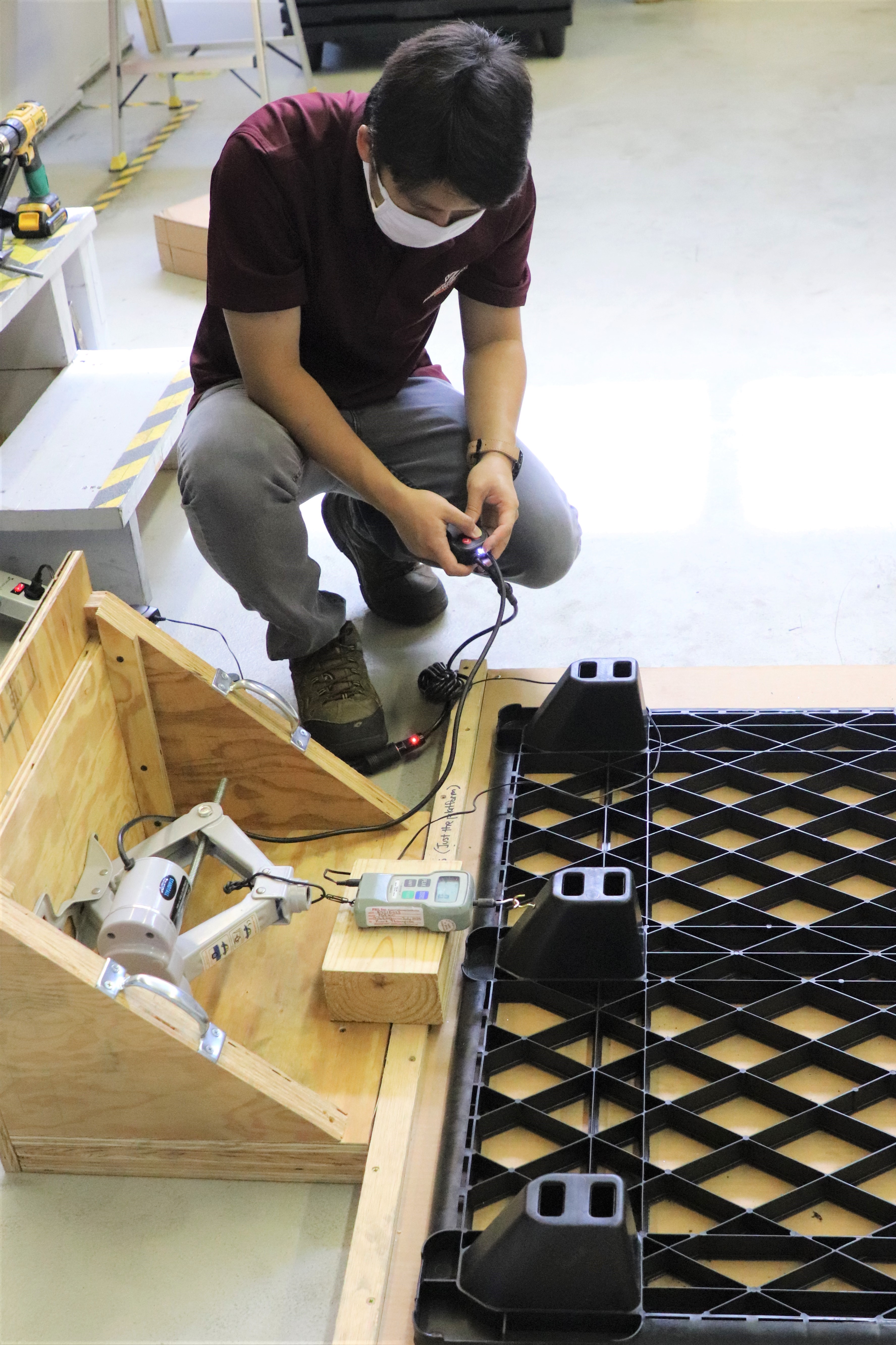
A custom jig was created to support the loaded pallet during dynamic testing. This consisted of a metal forklift carriage bolted to a steel assembly and a set of two 42 in. long fork tines that were hung from the carriage. The most conservative vibration profile collected during earlier research was used to simulate a dynamic forklift handling condition. To measure the deflection that the pallet experienced during the vibration test, up to string potentiometers were connected to the pallet and to the fork tines of the forklift simulator. Deflection values were recorded through a period of 30 minutes, or until the unit load collapsed.
The pallet deflection was measured and analyzed using three different variables (pallet orientation, unit load containment, and fork tine configuration). Then, an analysis of pallet deflection was conducted for each of the tested scenarios. A summary was provided with all the deflections observed at the beginning, at 3 minutes, and at 30 minutes of testing for those cases that the unit load survived for those amounts of time. For those cases where the unit load did not survive the entire test, the reported deflection was based on the time at which the unit load collapsed.
After 30 minutes of dynamic testing, the creep amount observed on the pallet for the bound unit load ranged from 15% - 33%. The creep deflection observed for the dynamic testing was much greater than it had been during the static testing (6%-13%). This indicated that the additional dynamic movement increased the creep and deflection of the pallet. A previous study conducted by Neville showed that when mechanical vibrations are applied to materials, it reduces the stress necessary to initiate yield strength in materials. In short, vibrations reduce the strength of materials. It follows that when vibrations were applied to the unit load, there was a jump in measurable deflection.
The creep amount for the pallet carrying the unbound unit load ranged from 36%-50% which is much higher than what was observed during the testing of the bound unit loads. This can be explained by the fact that the stretch film used for the bound unit load constraints the movement of the boxes, as well as the bending of the pallet. All three replicates of the unbound unit load under dynamic testing conditions did not survive the 30-minute test. Boxes fell off of the unit load at different timestamps, and it was observed that the failure of the unit load was usually seen on both sides of the pallet. The combined effect of the pallet and fork tines bending creates instability of the unit load (Image 4).
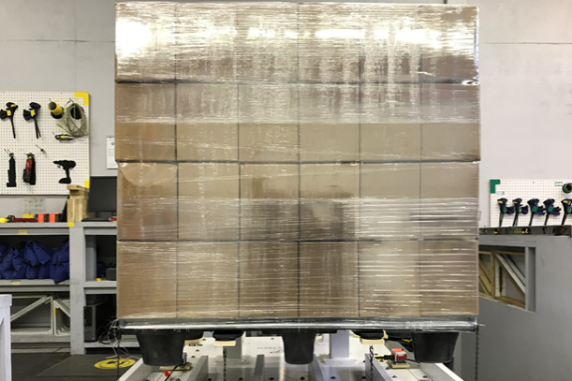
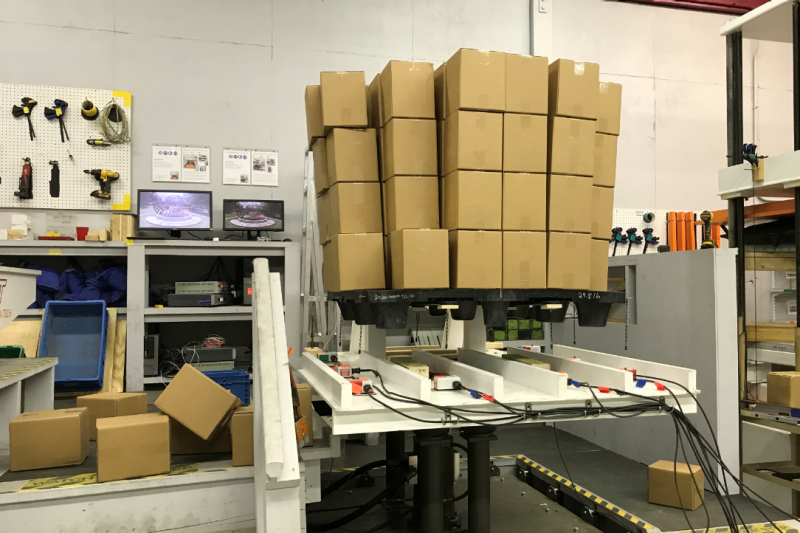
Forklift drivers have a tendency to tilt up the fork tines in order to create more stability on the unit loads. The maximum tilting of the fork tines measured for the forklifts was around 4°. Thus, in order to simulate this handling condition, both bound and unbound unit loads were tested in a static and dynamic conditions with level and with 4° angle fork tines. Overall, when comparing the creep deflections between level and 4° fork tines, it was observed that less deflection was measured using 4° fork tines in most of the locations on the pallet. This could be explained by the fact that the center of gravity was shifted towards the rear end of the pallet, and since there is no cantilever on the rear side of the fork tines it might have reduced pallet deflection.
Two out of three unbound unit loads under dynamic conditions with 4° fork tines did not survive the 30-minute test. The unbound unit loads with 4° fork tines only showed a creep deflection of between 17% and 23% which is less the same unit load on level fork tines. This could be explained by the fact that the center of gravity of the unit load is shifted towards the rear end of the pallet. Therefore, when dynamic motion is applied, part of the side bending of the unit load is distributed towards the rear end.
The conclusions obtained through the study were that:
- The highest deflection values were observed to occur on the front corners of the pallet due to the combined effects of deflection due to the cantilever of the fork tines and of the pallet.
- Vibration increases bending due to the magnification in the movement of the pallet.
- Fork tines do not creep during the different tests due to their rigidity, while pallet creeps over time, especially in the case of the unbound unit loads.
- Deflection limits proposed in the ISO 8611 standard are appropriate and potentially even too conservative for bound unit loads, but they are not appropriate for unbound unit loads.
- When the fork tines are not adjusted to stabilize the load (when they are level), the unit loads became unstable for both across the width and across the length orientations.
- When the operator tilts the fork tines back 4° the unit load was stable for the across the width orientation but not for the across the length orientation.
- Finally, the applicability of the ISO deflection limit depends on how the pallet is handled in the distribution.