Research Highlight: Investigation into the impacts and damages sustained by pallets during physical distribution
Image 1. Jorge Masis organizing pallets received from pallet recycling companies.
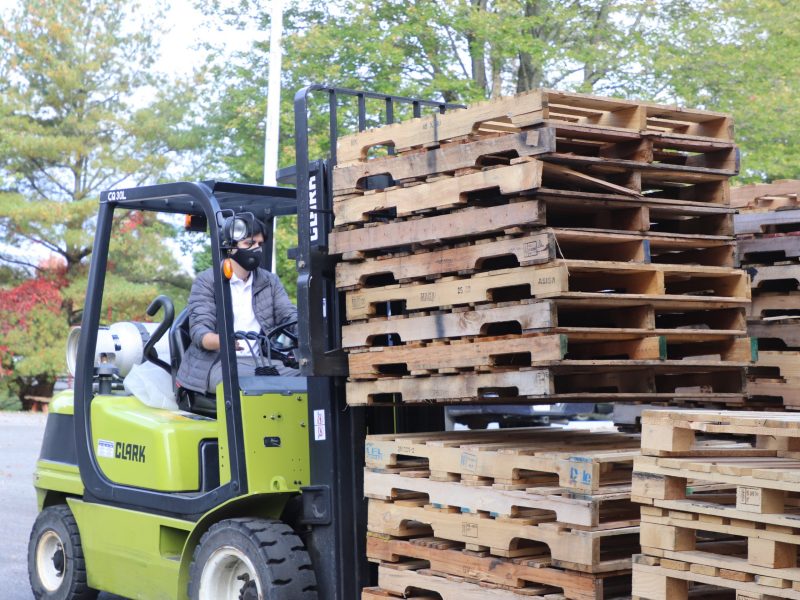
Master’s student Jorge Masís is looking into the damages that pallets sustain during their trips through the distribution supply chain and how closely these damages match those created during our accelerated pallet durability testing called FasTrack. Jorge’s research will be used to help update the FasTrack simulation to better represent a 21st century supply chain.
Image 2. Jorge Masis' graduate student picture with CPULD.
The end goal is for a pallet that has been run through the FasTrack durability tests in the lab to show the same damages as a pallet that has lived its useful life in a distribution supply chain. This will show that the FasTrack testing accurately predicts and mirrors what a pallet will actually experience.
The first step Jorge conducted was to collect and inspect the two different groups of pallets. The first was 306 used pallets that had been donated by three pallet recycling companies. The second was 265 pallets that had already been tested in CPULD’s FasTrack durability simulation. Jorge inspected all of the pallets that had been collected and recorded the number and types of damages seen on each pallet. Broken pieces, missing wood, twisted parts, and split boards are all expected as a result of the pallets’ interactions with the material handling environment.
To quantify the common damage modes and damage frequency as well as damage severity, a data collection tool was created and a collection methodology was developed. The data collection tool was divided into three sections: company characterization (listing either the pallet recycling company’s name or FasTrack), pallet characterization (including size, stringer/block, and other specifics), and damage characterization. This information was entered into the database for all 571 pallets.
Damages were identified according to both the Uniform Standard for Wooden Pallets developed by the National Wooden Pallet and Container Association and ISO 18613. Damages taken into consideration included splits, breaks, missing wood, and block twist.
Along with each damage type, a severity rating was issued. This severity scale takes into consideration the guidelines used to define damages for FasTrack. Medium-level damages, as defined for this study, take into account some damages that may not officially be considered “failures,” but the presence of these damages suggest that a component is being hit consistently. High-severity damages are those that could threaten the integrity of the packages being carried or affect the physical properties of the pallet in such a way that it can no longer serve its purpose and/or could create a safety hazard if it continues to be used.
The output of damages per pallet was analyzed for each source with Minitab 19. Histograms and Box Plots were developed with this tool as well as descriptive statistics for each source, including mean, standard deviation, and coefficient of variation, among others. To identify the behavior of the data, normality tests were performed according to pallet class to compare the resemblance of the data to the normal distribution. To identify differences among groups, the Kruskal-Wallis test for difference in medians was utilized.
Per the data collected to date, the FasTrack durability tests tend to cause more splits but fewer breaks than pallets typically experience during their useful lifespan. For stringer pallets, the most common damage mode was splits (59.4%) followed by missing wood (32.4%) and broken components (8.2%). Block pallets presented a same damage mode distribution with splits (57.1%) and missing wood (39.1%) being the most prominent damage modes. 2.7% of block pallets also experienced block twist for the 48 in. middle blocks.
Image 3. Damage modes observed for stringer and block pallet cores.
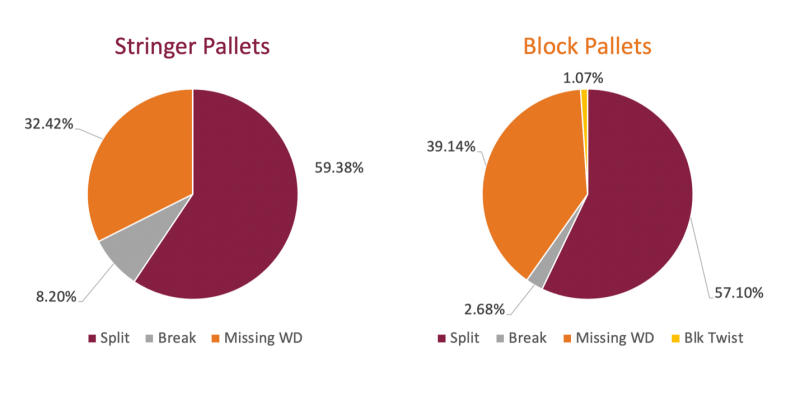
For both stringer and block pallets, most damages were concentrated for the top lead deckboards with 53.5% and 46.6% frequency, respectively. The second most common damage location was the bottom lead deckboard and side stringers for stringer pallets and bottom lead and bottom side board for block pallets. Damages to the bottom lead deckboards were most likely caused by forklifts because forklift drivers commonly lower the forks all the way to the ground when they try to pick up a pallet. The results of Virginia Tech’s Fastrack simulation shows that adding chamfers to the bottom lead board can mitigate some of these damages. Block pallets experienced damages to their bottom side boards as well because block pallets have full four-way accessibility thus forktines can often hit the sides of the pallet during handling.
The study also investigated two different damage severity levels (medium and high). The results showed that the split between medium and high damages is about 50-50 for both pallet designs. In addition, most of the investigated components experienced the same number of medium and high damages. When the damage mode as a function of a pallet component was investigated, it was found that both block and stringer pallet top lead deckboards were mainly damaged due to splits and missing wood (which is most likely the consequence of splits too).
Image 4. Damage modes experienced by block pallets for the different pallet components.
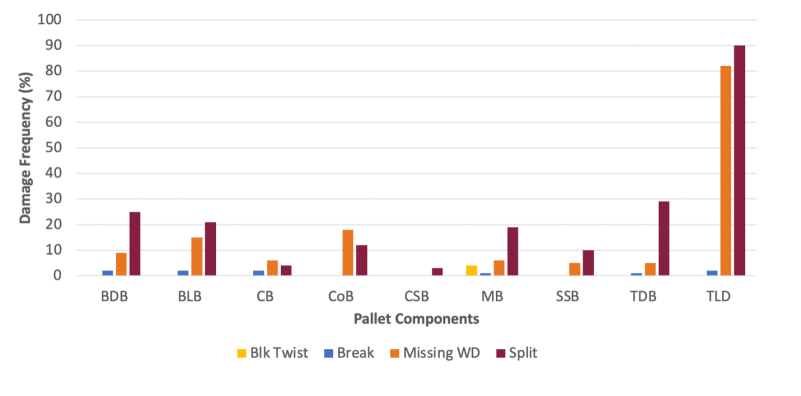