COVID19 has brought new procedures to CPULD's classes and labs
Image 1. Lecture on over-the-road vibration of sensitive electronics.
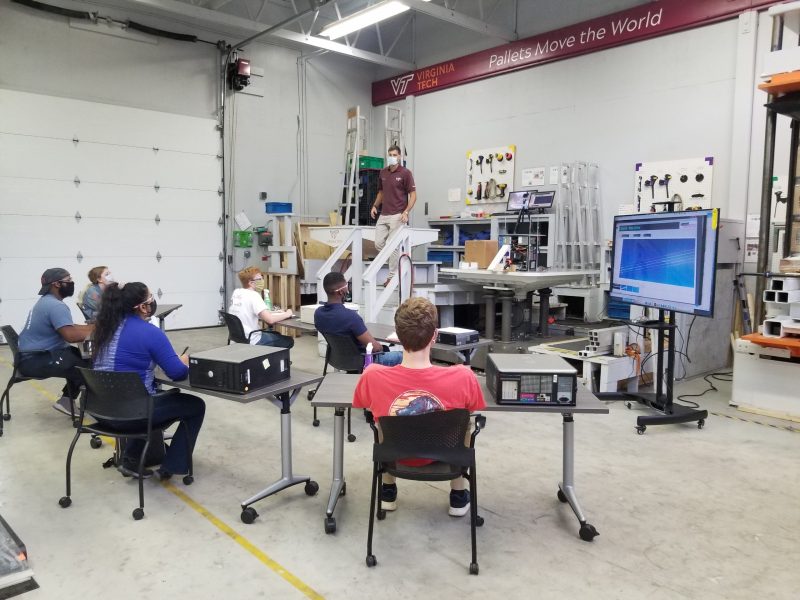
The COVID-19 pandemic has changed the way the packaging program at Virginia Tech educates students. Our packaging program is currently ranked No. 4 in the U.S. We focus on educating future packaging professionals using a hands-on and minds-on approach. Our program’s coursework is heavily focused on hands-on laboratories and semester-long projects to ensure that each of the skills that the students are learning is translated into practical applications. Through the Center for Packaging and Unit Load Design, students also have the chance to work on real-life, company-sponsored packaging design and research projects. These projects allow students to work on relevant problems in the industry and to come up with solutions that could eliminate damage, increase effectiveness, and improve the sustainability of packaging.
The SBIO 4024 Packaging Design for Global Distributions course focuses on teaching students how to design protective packaging solutions that can survive the hazards of global physical distribution. The cornerstones of this course are the laboratory exercises and the semester-long redesign projects, both of which require the students to be physically present in the lab and use the equipment. In 2020, the maximum number of students in each course laboratory section decreased to six, and students had to keep 6 feet apart. All of this created new challenges for course delivery.
To overcome these challenges, Associate Professor Laszlo Horvath used digital technology to develop live laboratories that still allowed students to have high-quality, hand-on experiences with vibration and shock testing. During lab session, Dr. Horvath showed students how to simulate over-the-road transportation for highly sensitive electronics and how to identify critical elements such as memory units or graphic cards that could be damaged by the vibrations. To allow for social distancing, multiple webcams were used to stream the critical information to a 65-inch TV, which allowed students to see the vibration levels for different components from a distance.
Instrumented packages filled with shock sensors also allowed us to capture and present impact data during drop sequences simulating Amazon’s distribution network. Students learned how to use the drop tester and to identify shock events from corner, edge, and face drops.
Image 2. Lecture using instrumented packages to measure impacts during the Amazon 6A drop sequence testing.
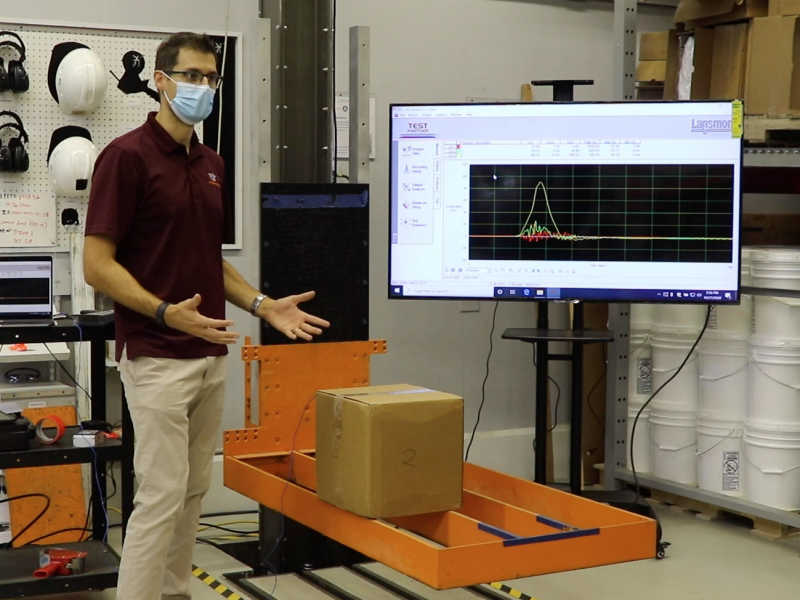
In order to teach students how to set up sensors in transportation devices and then collect and analyze the shock and vibration data from distribution, Dr. Horvath partnered with Lansmont Corporation. He used their state-of-the-art 3D15 and 9x30 remote data acquisition units to instrument a Penske truck and then collect data from their Blacksburg-Charlotte-Blacksburg and Blacksburg-Dublin-Blacksburg routes. The truck was instrumented with two different sensors to measure shock and vibration as well as two GoPro cameras in order to have video footage from the trips. After the data was collected, Erich Joneson, Lansmont’s data analysis guru, joined the class remotely to teach students how to extract the needed information from the collected data.
Image 3. Shock data obtained from the recorded trip with a Penske truck.
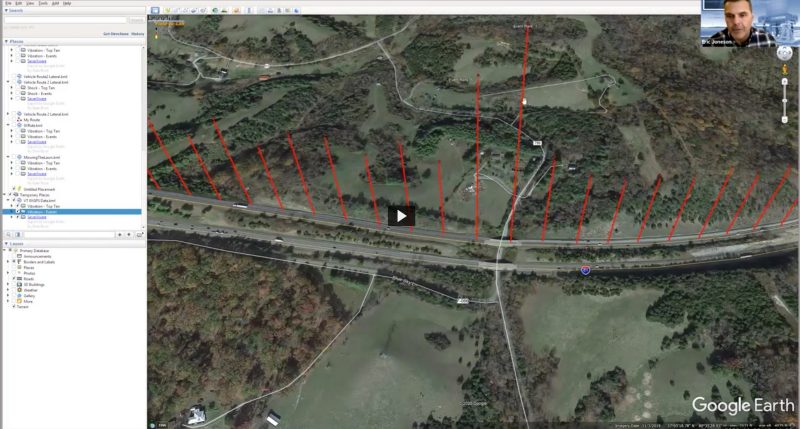