Investigation into the effect of various factors on the vibration levels experienced by unit loads under forklift handling conditions
Image 1. Yu Yang Huang attaching sensors to the electric-powered forklift.
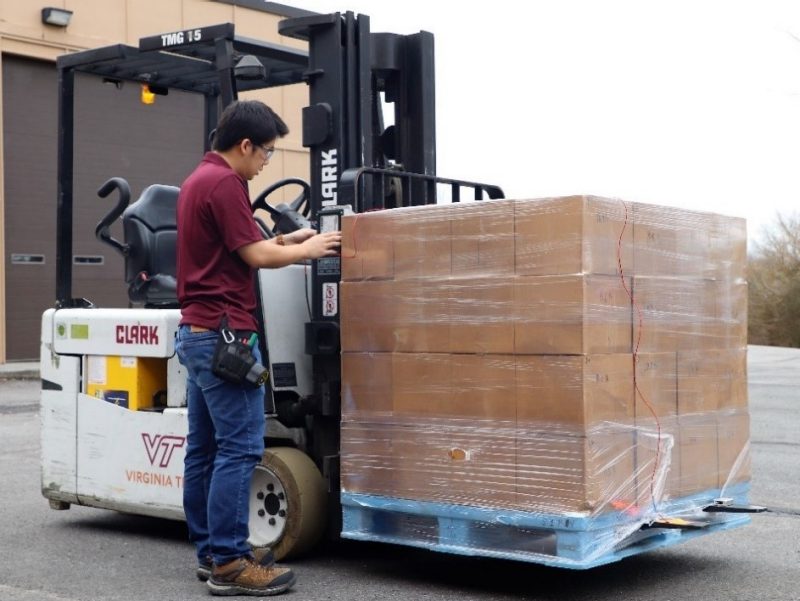
Forklifts play an important role in the global distribution of packaged products. They are commonly used to move and lift materials and products throughout the supply chain and offer load capacities from a few thousand pounds up to 180,000 pounds. Forklifts are one of the most common types of material handling equipment used in warehouses and distribution centers.
Forklifts experience vibration during operation. Vibration is a mechanical phenomenon that is very common in transport vehicles and affects every packaged product during the handling and transportation process. Forklifts experience different vibration levels under different conditions, such as speed, road conditions, and unit load weight. The vibration produced is not a smooth, oscillatory motion; it is a shaped mix of various frequencies and amplitudes, and it is constantly changing.
Forklifts are the most common material handling method used to move pallets through the supply chain. While being transported on a forklift, pallets have a different load capacity, commonly referred to as dynamic load capacity. Despite the term “dynamic,” current testing standards only use static load tests to measure this value. Master’s student Yu Yang’s research focuses specifically on developing a true dynamic load testing method for pallets and then using this new method to revise the ISO 8611 testing standard.
While many studies have been done analyzing the vibration levels of forklifts, not much research has been conducted to analyze how various factors affect vibration. The goal of the first phase of Yu Yang’s research was to understand how the vibration experienced by unit loads while being transported on forklifts is affected by speed, road conditions, unit load weight, forklift type, and sensor location. For this research, several power spectral densities (PSD) were obtained and analyzed for different types of commonly used industrial forklifts in a laboratory environment.
Image 2a. Gas-powered forklift.
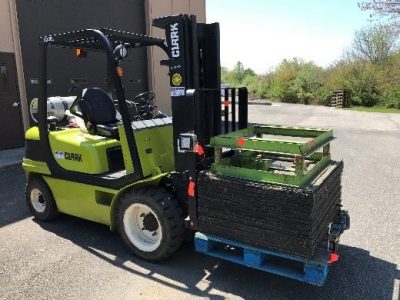
Image 2b. Electric-powered forklift.
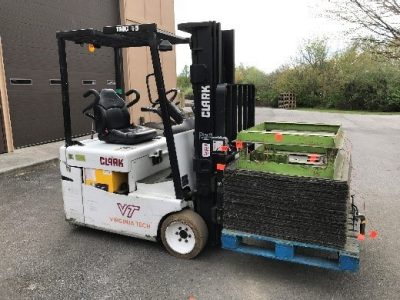
Image 2c. Reach truck.
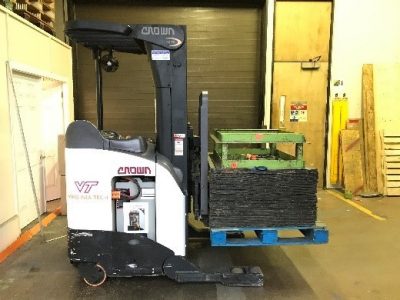
Three types of forklifts were investigated (gas-powered, electric-powered, and a reach truck) on two different types of road conditions (concrete and asphalt) while carrying two different load weights (1,500 lbs. and 2,500 lbs.). The intensity of vibrations caused by the forklifts was measured using a Lansmont SAVER 9X30 data logger under the various handling scenarios. Two three-axis accelerometers were also connected to the data logger to record data from three different positions of the forklift.
Image 3. Sensor positions for the vibration data collection.
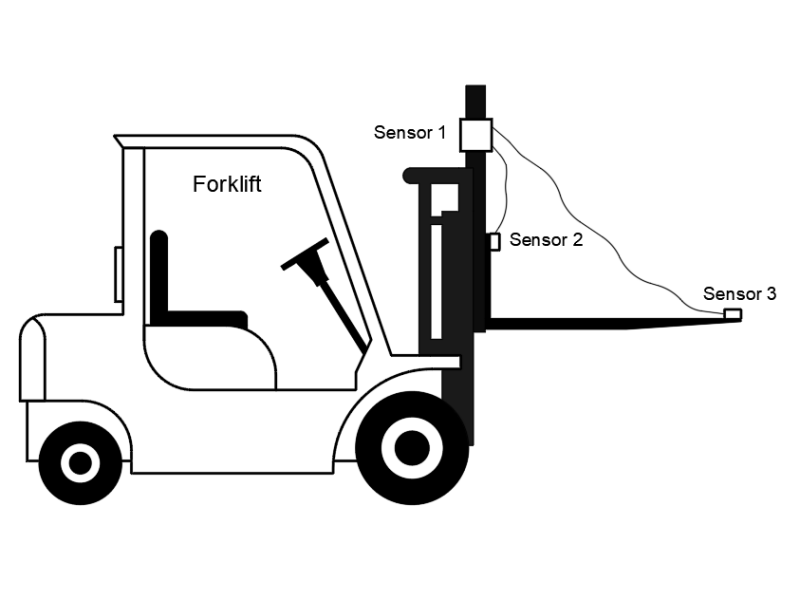
An analysis of vibration levels was conducted using Grms (root-mean-square) values and power spectral density plots. An initial analysis using Grms values was conducted to compare the vibration levels that were generated by the three forklifts under the different handling scenarios. A second analysis used the power spectral density plots to analyze in more detail the effects of speed, road condition, forklift type, unit load weight, and sensor location on forklift vibration levels. Furthermore, a comparison of vibration levels was performed between an ISTA trailer truck and the forklifts.
It was observed that the gas-powered forklift presented the highest vibration intensity while the reach truck showed the least. The highest peaks were observed on low frequencies, around 3.5 Hz. The gas and electric forklifts presented peaks near the same frequency, while the peaks for the reach truck shifted towards higher frequencies.
It was discovered that forklifts on asphalt experienced a higher level of vibration compared to forklifts on concrete. The results also revealed that the sensors, at both the carriage and the tip, measured increasing vibration levels with increasing speed. The change in speed represented an increase in vibration levels of 41.6% on asphalt and a 38.4% on concrete. Vibration levels at the tip of the tines were higher than those at the forklifts’ carriage.
Additionally, it was observed that, on all three forklifts, the vibration levels decreased with an increase in the weight of the unit load. For the gas and electric forklifts, the highest peaks occurred at low frequencies around 2.0-4.0 Hz. For the reach truck, the highest peaks occurred around 3.0-5.0 Hz. The peaks of vibration shifted towards lower frequencies with increasing weight. The change in the weight represented an increase of 26.0% on asphalt and 7.2% on concrete.
Image 4. Comparison between an ISTA trailer truck and forklifts in vibration levels experienced.
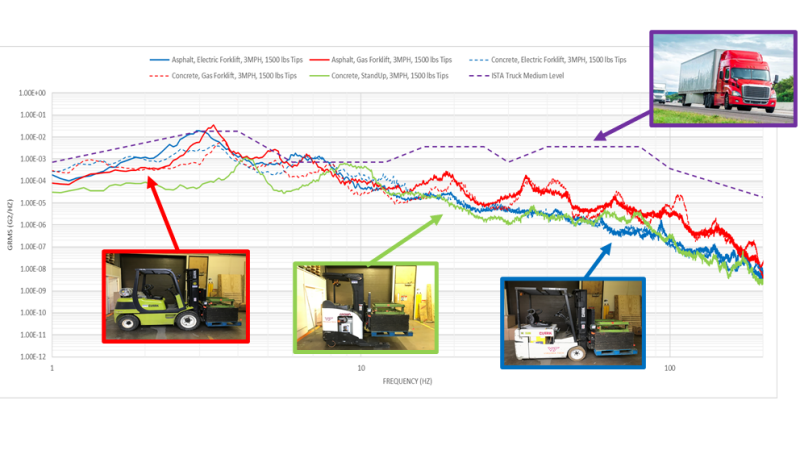
Finally, it was found that ISTA trailer trucks experience higher vibration levels compared to forklifts. Vibration levels are affected by the suspension system of the vehicle. The suspension system is connected to the wheels, which provide contact between the road and the vehicle. The type of suspension and the speed of the vehicle affect vibration levels. In previous studies, researchers concluded that air-suspended trailer trucks experience the lowest level of vibration on a continuous road surface which, in turn, transmits the lowest level of peak accelerations to the cargo. In addition, they mentioned that the damping of this vehicles’ suspension is superior to trucks having steel spring suspensions, resulting in a quicker recovery from severe shocks.
In short, the results showed that an increase in forklift speed increases vibration intensity. On the other hand, an increase in the forklift load weight decreases vibration intensity. Among the three forklifts studied, the gas-powered forklift has the highest Grms values on an asphalt road surface.
The next phase of this research will focus on using the obtained information to create a dynamic pallet bending measurement method on our vibration table.