CPULD partnered with NWPCA to offer a webinar on fasteners and their use in pallet construction
Image 1. Example of product damage caused by fastener failure.
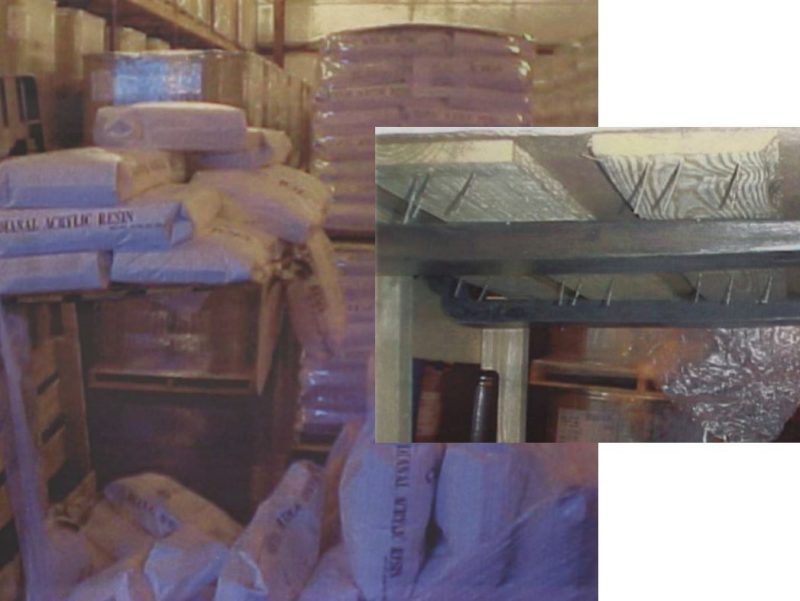
The Center for Packaging and Unit Load Design partnered again with the National Wooden Pallet and Container Association (NWPCA) on November 17 to offer a free webinar for members of either organization. The short course attracted over 50 attendees from multiple countries to the live webinar. The recording, including the question-and-answer portion, is being offered free to the public on YouTube (PDS Basics – Fasteners) through the end of this year. In 2021, it will be available only to members of NWPCA, so take the opportunity to watch this interesting lecture while it is available to everyone!
Brad Gething, director of science and technology integration at NWPCA, and Laszlo Horvath, director of CPULD, spoke about fasteners — their specifications and their use in pallet construction. Fasteners comprise only 5% of the cost of a pallet, but they can have a major impact on a pallet’s durability, strength, and stiffness level. And when fasteners fail, products get damaged.
There are many different types and sizes of nails that can be used in pallet construction, but the most commonly used types are helically threaded and annularly threaded nails. Dr. Horvath spoke about many different aspects of fasteners and offered tips such as why to use annularly threaded nails in softwood components and helically threaded nails in the hardwood species. Using NWPCA’s Pallet Design System (PDS) software can help decision-making during the pallet design process by filling in all the specs for the fasteners you’ve chosen, informing you how the selection will affect your pallet.
Pallet durability is the main issue for all design decisions. Since the 1970s, the formulas used to calculate pallet durability have included nine different factors; the first three of those factors directly relate to the fasteners used. Shank withdrawal, shearing, and head pull-through are the potential modes of failure, but they can be predicted and accounted for during the design process.
Image 2. Fastener failure modes.
The press-out of a fastener (the difference between the wire diameter and the thread-crest diameter) and its thread angle (calculated by the number of helixes and the thread length) are the main parameters that define the nail’s withdrawal and pull-through resistance. Thread press-out has the most direct effect; increasing the press-out by just .015 in. can increase the fastener’s withdrawal resistance by 55%. And decreasing the fastener’s thread angle from 68 degrees to 60 degrees can increase withdrawal resistance by 34%. But a lot more factors than these go into the formulas for fastener testing. The species of wood and the thickness of the boards being used as well as the moisture content of the lumber all contribute to the fasteners’ strength. Additionally, the number of fasteners per connection affects their individual strength.
Shearing is the result of fasteners that are too thin and/or aren’t stiff enough. While fasteners’ withdrawal and pull-through resistance can be calculated from their manufacturing specs, the shear resistance is something that must be physically tested to find. The number needed for figuring the shear resistance is called the fasteners’ MIBANT angle, which is basically its resistance to dynamic impacts.
Image 3. MIBANT testing equipment.
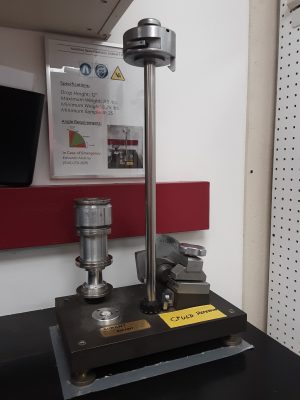
The Uniform Standard for Wood Pallets (2014) includes requirements for how many and what types and sizes of fasteners to use as well as what their withdrawal, pull-through, and shear resistance numbers should be. This standard states other specifics as well, such as how deep a fastener must penetrate the stringer (at least 1 in.), the minimum head-to-shank ratio of the fasteners being used (2.00), and the number of fasteners per deckboard connection (deckboards less than 5.25 in. wide require at least two fasteners while wider deckboards can require up to four).
At the end of the webinar, the presenters took questions from the attendees. Dr. Horvath spoke about the Virginia Tech research that backs up the MIBANT angles and press-out requirements and the most common fastener failures. He mentioned that fastener quality has decreased significantly over the years; 20 years ago, a fastener that would have been labeled “poor quality” is now considered “good” because average fastener quality has declined so much. But, as Dr. Gething points out, the PDS software can take a lot of the guesswork out of fastener choice because it will do all the calculations for you and let you know exactly what to use to get the durability ratings you want on a new pallet design.
The Center for Packaging and Unit Load Design offers a wide range of pallet fastener testing services and works with companies to eliminate the chances of nail failure in the distribution chain. For more information, visit https://www.unitload.vt.edu/facilities/fastener-testing-lab.html.
Watch the recording of this webinar to learn even more about fasteners and their effects on pallets! https://www.youtube.com/watch?v=kQmtB34mUvI&feature=youtu.be