An Operational Concept of an IoT System for the Palletized Distribution Supply Chain
Figure 1 Concept of Operations illustration on how the system with IoT sensor could function.
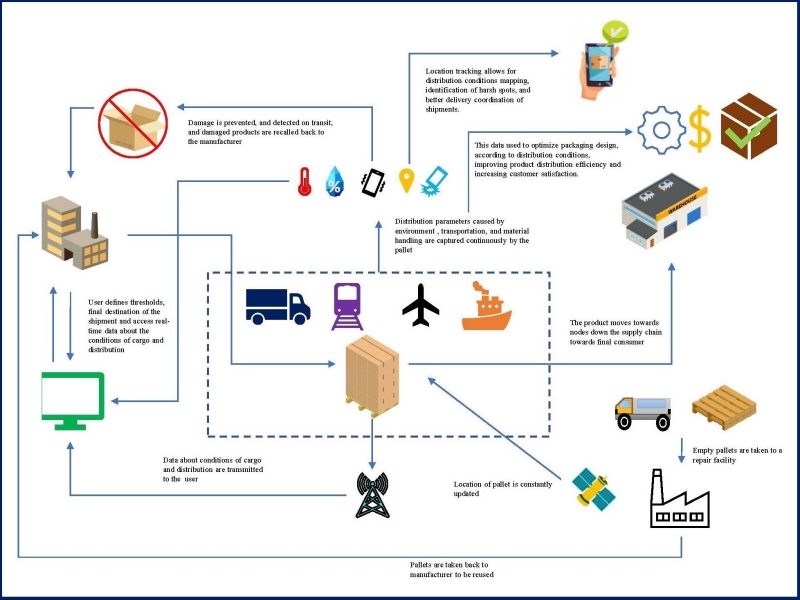
Distribution implies that products are interacting with multiple external conditions, including known hazards: shock, vibration, compression, and atmospheric. The role of distribution packaging during the distribution of products along the supply chain is to minimize the negative effects that these hazards pose to the products being transported and help guarantee that the product reaches the customer in an acceptable condition. However, due to the variability of distribution channels, there is a high level of uncertainty associated with which distribution hazards are present during a specific supply chain’s handling and transportation of products. Established pre-shipment testing protocols for packaging are limited in their capacity to accurately simulate the real-world conditions that occur in specific supply chains, which has resulted in suboptimal packaging designs.
This study, conducted by master’s student Nicolas Navarro, surveyed industrial companies and found that they are most concerned with avoiding damage to their products during transportation as a result of temperature, relative humidity, shock, and vibration. It was also discovered that there is a great desire among companies to increase the visibility of the movement of their products along their supply chain.
This project puts forth the theory that, by having greater certainty about the conditions present in their specific distribution supply chain, it would be possible for companies to design more efficient and effective packaging solutions for any given product. In order to achieve this certainty, this research proposes a system that uses Internet-of-Things (IoT) technology, namely sensors, to capture data about the conditions in a company’s specific distribution environment in order for a company to be able to design packaging and systems that perform better and that satisfy their needs relating to product protection during distribution.
Pallets are a key component of distribution operations in supply chains, as they are the main interface that connects material handling equipment and packaged products. Based on this distinctive characteristic, this research contends that pallets would be effective carriers for IoT devices; therefore, they could be used to gain insight into the realities of what is experienced by a company’s products and packaging during distribution. This will eventually allow for more customized and optimized packaging designs supported by more reliable and representative information.
Using a model-based systems engineering approach, a Concept of Operations (ConOps) was proposed to show what is needed to be able to track all of these conditions and parameters. The ConOps illustrates the way something is done at the current time as opposed to how it will be done in the future after implementing internet-of-things (IoT) technologies (Image 1). Furthermore, the application of a systems engineering framework makes it possible to lay out a clear value proposition for the adoption of new IoT technology in the field of distribution packaging and supply chains so there is higher certainty that the new system will be responding to genuine user needs.
In order to achieve its purpose, a proposed IoT system must interact with the physical environment and collect the inputs for the distribution parameters. This research project divided system interactions into five different types and represented them using sequence diagrams.
- A pallet pairing and input definition sequence diagram focuses on the interaction between the user and the system. As part of this interaction, the pallet containing the IoT device is linked to the user’s account, the required thresholds are defined, and a final destination is specified that will indicate to the system to stop recording.
- A distribution parameters recording sequence diagram outlines which parameters need to be monitored continuously throughout transportation, such as temperature, relative humidity and location.
- A distribution events tracking sequence diagram (Image 2) focuses on outlining variables that only need to be recorded once a critical threshold is exceeded, such as shock or temperature and humidity extremes.
- The recording of vibration data was separated into its own sequence diagram because of the enormous amount of data that needs to be collected in order to build a useful vibration profile. But to conserve battery life and data storage, this research proposed a way to collect only the minimum amount of vibration data needed to construct a representative vibration profile. Basically, a procedure was developed to ensure that only meaningful, representative vibration data is collected.
- The final sequence diagram used in the system is for monitoring environmental parameters. This is when a user creates an inquiry to the system and the system then shows them all of the collected data so far on the shipment.
Figure 2: Sequence diagram for distribution event tracking.
From a physical point of view, the system is composed of two basic elements: the smart sensor and the software platform that uses, stores, and transmits the data that the sensor collects. A smart sensor is the device that measures the physical parameters of processes or environments; it is what makes possible the execution of the needed functions. However, sensors alone cannot provide end-to-end supply chain visibility. They need an entire cyber-physical-system that involves the software platform as well as a means of connectivity to process and transmit the data collected. The software platform is the component by which data is transmitted and the collected information is conveyed to the user.
The study also explored the potential challenges that companies could be faced with during the implementation of the proposed cyber-physical technologies such as security concerns, the energy requirements of IoT sensors, service life, sensor location on the pallets, and computational requirements.
The study found that leveraging on model-based systems engineering works for this application because it allows the users to utilize the complexities presented by the nature of IoT technology so that the system developed is more likely to meet the requirements necessary to satisfy the user’s needs. Furthermore, the application of the systems engineering framework makes it possible to lay out a clear value proposition for the adoption of a new technology, like IoT, in the field of distribution packaging and supply chain, so there is higher certainty that the new system will be responding to genuine user needs.