Research Highlight: Evaluation and redesign of packaging for an AC unit with a focus on sustainability
ac unit
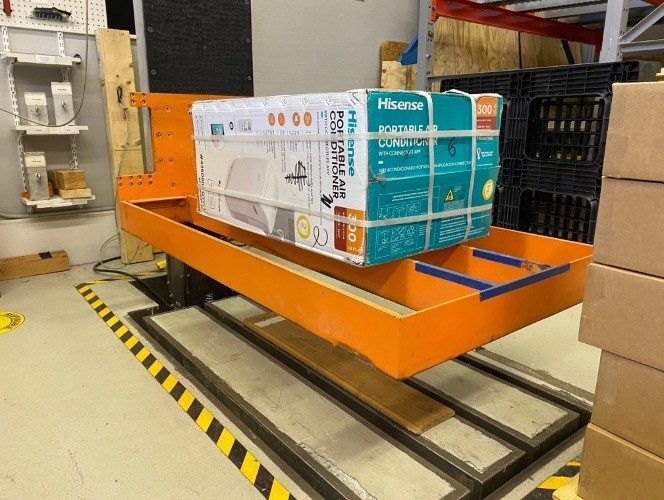
CPULD believes in hands-on and mind-on education thus with the help of our corporate partners each year a group of undergraduate students are working on real-life industrial packaging design projects. The focus of 2023 Spring project was on the packaging redesign of a Toshiba portable air conditioner. Currently, the interior packaging of the portable AC unit consists of two Expanded Polystyrene (EPS) inserts that mold to the top and bottom of the unit. The project sponsor’s interest is in switching to a more sustainable packaging solution. They tasked this research group with exploring sustainable options and if they could be used with similar cost and performance levels.
The first step in tackling this problem involved testing the current packaging that is used for this AC unit. The idea was to give a baseline from which to compare the performance of future prototypes. The testing procedures for the baseline and subsequent prototypes followed the ISTA Amazon 6B standard which simulates the hazards and damage that packages are susceptible to along the supply chain.
For this project, each package had to endure five separate ISTA test sequences before being considered a pass or fail. The first tests were drops and were a variety of edge, corner, and face drops (Image 1). The next test was a horizontal clamping test with wooden plates to separate the unit from the tester. The package was required to overhang 3 in. off the wooden plates in both directions and the standard requires clamping the unit at quadruple its weight, giving us a clamping force of 292.8 lbs. The third test was a vertical compression test that was meant to imitate the weight a package would endure when being stacked in a warehouse. It is a good indication of the package’s stacking strength. Next in line was the series of vibration tests. These tests are simulations of the vibrations that a package would experience in the back of a truck and when they are being picked up and delivered (Image 2).
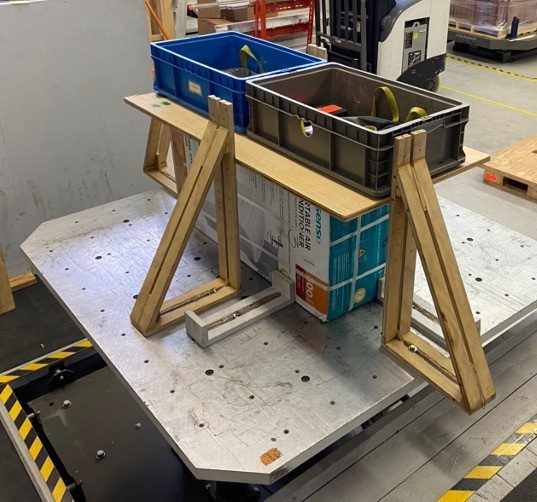
After testing the original packaging thru these steps, the researchers began creating prototype packages for the AC unit (following the goals of less materials and sustainability). Their first attempt did not survive even the first set of drop tests, but they learned quickly and each subsequent prototype performed better. The two tests that did the most damage to the final prototype were the compression and vibration tests. The compression test completely buckled some of the edges and corners of the prototype packaging. The vibration tests amplified this buckling of the box, especially on Face 6, where the flaps were bent open.
At the end of the project the new packaging made of fully curbside recyclable protective packaging had equivalent performance than the original baseline. Also, the students calculated the cost of the prototype packaging system to be only $12.19 in materials which is only 3.5% of the current selling price of the product.
The students were able to show the sponsor that moving to a more sustainable solution in the future benefits everyone without compromising performance and cost.