Research Highlight: Looking at the Correlation of Pallet Stiffness to Box Compression Strength
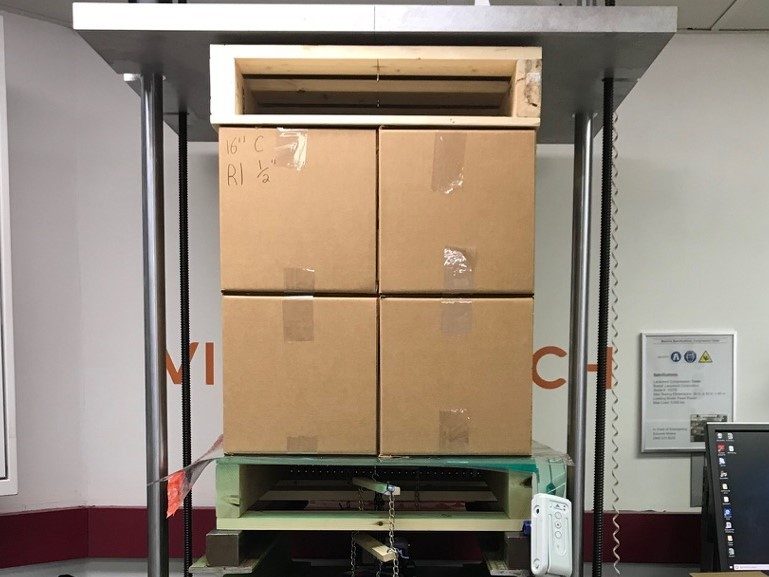
Packaged products are primarily shipped as unit loads that consist of products packaged in corrugated boxes restrained to a platform, commonly a pallet. Paying particular attention to the design of the unit load components is necessary to safely ship products while still maintaining low packaging costs and sustainability initiatives. Stacking unit loads is a common practice to effectively use warehouse space, but the packaging must support large amounts of weight when pallets are stacked. Pallets are not completely rigid and will deform because of this weight, which creates an uneven top deck surface resulting in asymmetrical support of the corrugated boxes. The level of this unevenness can significantly affect the strength of the corrugated boxes.
The amount of bending experienced by the pallet can be controlled during the design of the pallet. For example, using thicker top deckboards will result in a stiffer pallet deck. Further, altering the species of lumber used or the number of stringers in the design of the pallet can have a similar effect. To further investigate how pallet top deck stiffness affects the strength of corrugated boxes, the Industrial Membership of the Center sponsored a research project from May 2018 through December 2019. Chandler Quesenberry worked on this research project as part of his M.S. thesis.
The purpose of the research project was to investigate the effect that pallet stiffness has on the compression strength of corrugated boxes. Specifically, this research looked at how different variations of pallet top deck stiffnesses, and the resulting asymmetric support, affects corrugated box compression strength (Image 1).
The results indicated that pallet top deck stiffness has a significant effect on box compression strength. Compression tests were completed on boxes supported by pallet designs having different top deckboard stiffnesses. Pressure data recorded between the bottom layer of boxes and the top of the pallet showed that a larger percentage of the pressure was located towards the outside edges of a unit load of boxes that were carried by a flexible pallet. A thicker deckboard, acting as a simply supported beam, deflects less than a thinner deckboard under the same unit load. And when the pallet top deck stiffness increased, the compression strength of corrugated boxes increased as well. There was actually a 29% to 35% increase in box compression strength found for the boxes supported by high stiffness pallets compared with boxes on low stiffness pallets (Image 2).
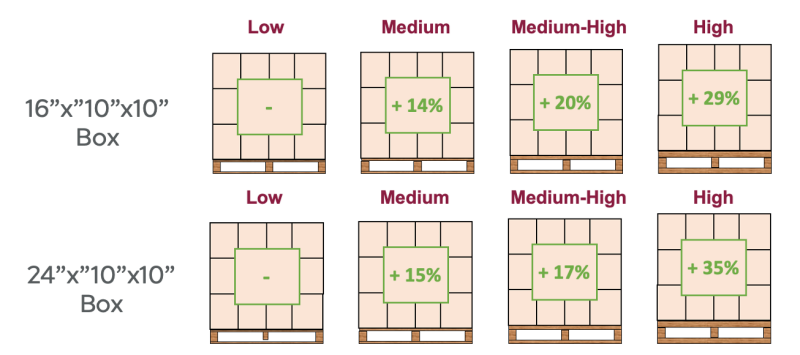
The fact that boxes were weaker on low stiffness pallets is explained by the uneven pressure distribution between the top deckboard of the pallet and the bottom layer of boxes. Pressure mat data showed that a higher percentage of total pressure was located under box sidewalls that were supported on the stringers of low stiffness pallets compared with high stiffness pallets. This was disproportionately loading one side of the box, causing premature package failure.
A certain compression strength of a palletized box can be attained by redesigning the unit load in multiple ways. Conventionally, the means of changing the compression strength of boxes is by adjusting the corrugated board grade and flute type. But, using systems-based design methodology by utilizing the pallet top deck stiffness effect on box compression performance, it is possible to deliver similar changes to compression strength of boxes without changing the boxes themselves. When boxes are supported by a stiffer pallet, the boxes have increased compression strength/performance similar to, or even greater than, when the boxes’ board grades are changed. Both approaches result in compression strength gains, but one design changes the box cost and the other design changes the pallet cost.
The project also included a financial analysis that revealed that when higher stiffness pallets are used, the cost of the corrugated boxes could actually be reduced, resulting in a reduction of the overall cost of the unit load by as much as $1.84 (Image 3). Therefore, pallet and packaging designers can use pallet top deck stiffness levels to their advantage as an option for cost cutting when redesigning corrugated boxes.
This study revealed that the level of pallet top deck stiffness should be addressed during the box design process. Designers can use pallet top deck stiffness to their advantage as an option for cost cutting or redesigning corrugated boxes if they can control what stiffness level of pallet is being used for their unit load shipments. The pallet top deck stiffness should be included as an adjustment factor for current design methodologies similar to other box-pallet factors such as pallet gaps, overhang, pallet pattern, and stacking alignment.
Chandler Quesennberry successfully defended his M.S. thesis in December 2019 and is now working for The Pallet Alliance as a pallet program and design specialist using the knowledge that he obtained during his studies to help his company save money on unit loads through their pallet designs.